Introduction
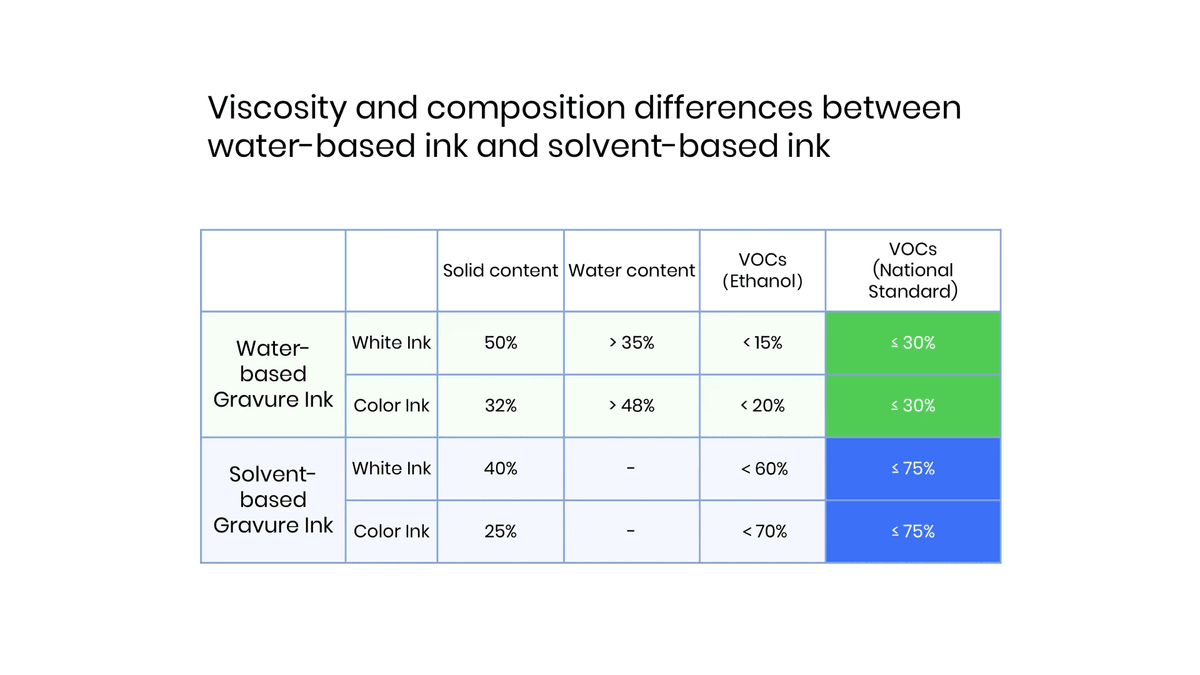
In the world of packaging inks and coatings, the choice between water-based ink, solvent ink, and UV ink can be a daunting task. Understanding the differences between water-based ink and solvent-based ink is crucial for selecting the right ink for your printing needs. Key factors such as print quality, color vibrancy, versatility, and cost efficiency play a significant role in making informed decisions when it comes to packaging inks.
Understanding Water Based Ink and Solvent Based Ink
Water-based ink is known for its eco-friendly nature, low VOC emissions, and easy clean-up process. On the other hand, solvent-based ink offers fast drying times and excellent adhesion to various substrates. Both inks have their unique advantages and disadvantages, making it essential to weigh these factors when choosing the right ink for your specific printing project.
Choosing the Right Ink for Your Printing Needs
When it comes to packaging inks, one must consider the compatibility with different substrates, flexibility in printing techniques, adaptability to various packaging requirements, and overall impact on packaging aesthetics. These considerations are crucial in ensuring that the chosen ink meets all the necessary requirements for a successful print job.
Key Factors to Consider When Selecting Ink
Color accuracy and vibrancy are key factors that directly impact the visual appeal of packaging materials. Longevity and resistance to fading are also critical for maintaining product aesthetics over time. Additionally, production speed, drying time, operational expenses, and overall cost-effectiveness should be carefully evaluated before making a final decision on which type of ink to use.
Composition and Properties
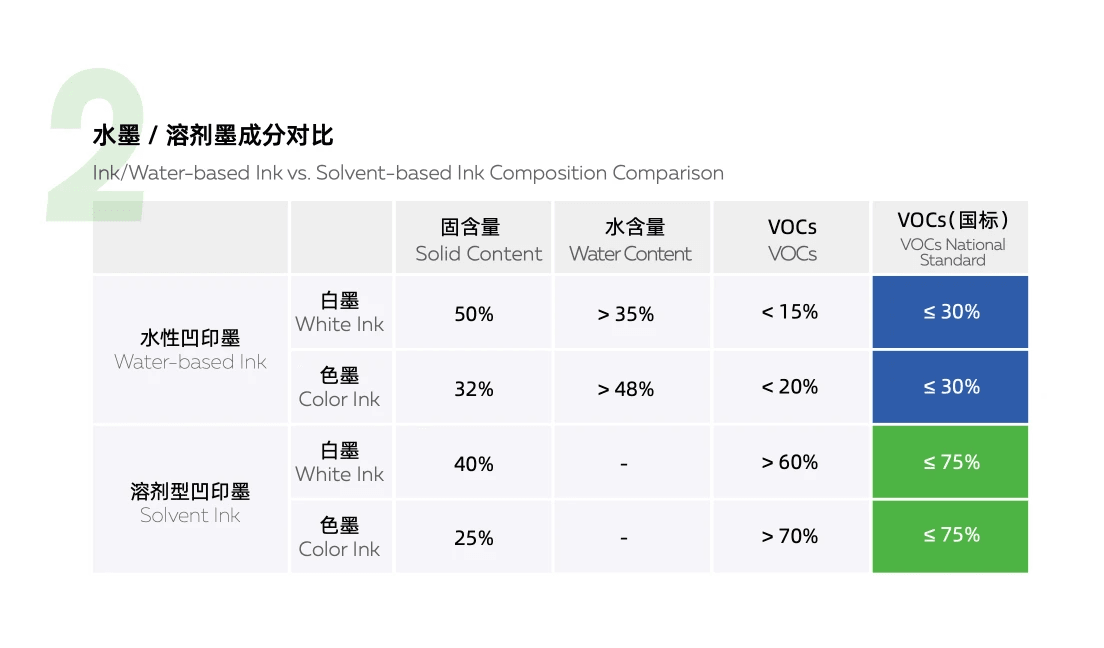
Water Based Ink V.S Solvent Based Ink is a crucial decision in the packaging inks and coatings market, with each type offering unique benefits. Water-based ink, as the name suggests, uses water as a primary solvent, making it eco-friendly and safe for use. On the other hand, solvent ink contains volatile organic compounds (VOCs) that require proper ventilation during printing.
Chemical makeup and drying process
Water-based ink typically consists of pigments or dyes dispersed in water along with additives like binders and surfactants. It dries through evaporation, making it suitable for absorbent substrates like paper and cardboard. Solvent ink, on the other hand, contains organic solvents that evaporate during drying, leaving behind the pigment or dye on non-absorbent materials like plastics and metals.
Environmental impact and safety considerations
The environmental impact of Water Based Ink V.S Solvent Based Ink is significant, with water-based ink being more environmentally friendly due to its lower VOC content and reduced air pollution. Additionally, water-based inks are safer for workers to handle compared to solvent-based inks because they don't emit harmful fumes during printing.
Qinghe's Waterborne Polyurethane Inks
Qinghe's Waterborne Polyurethane Inks are a prime example of innovative water-based inks that offer excellent adhesion, flexibility, and durability on various substrates while minimizing environmental impact. These inks provide vibrant colors without sacrificing print quality or performance.
Application Demonstration
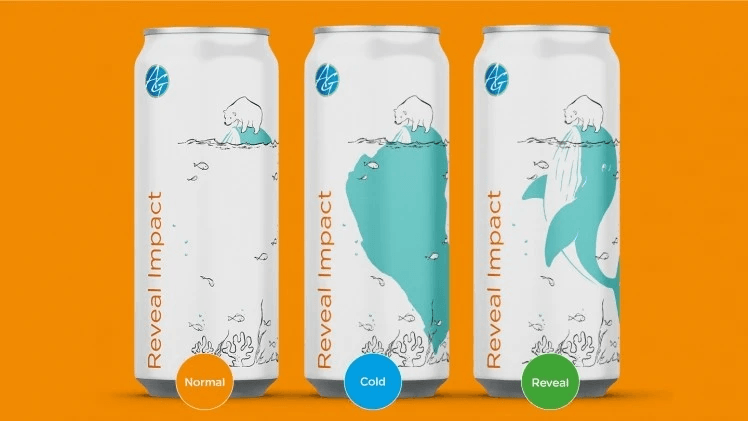
When it comes to printing on PVC shrink film for dry and wet bottle labels, the choice between water-based ink and solvent ink is crucial. Water-based ink offers a more environmentally friendly option with lower VOC emissions, while solvent ink provides faster drying times and greater durability against moisture. UV ink is also a viable alternative for its instant curing capabilities, making it suitable for high-speed production lines.
PVC Shrink Film (for Dry and Wet Bottle Labels)
For dry and wet bottle labels, water-based ink proves to be a sustainable choice, as it offers excellent adhesion to PVC shrink film while minimizing environmental impact. On the other hand, solvent-based ink provides superior resistance to moisture and abrasion, ensuring long-lasting print quality on bottle labels.
Matte Ink (Wear-resistant, Heat-resistant, Water-resistant)
When it comes to matte ink for packaging applications, both water-based and solvent-based options offer wear-resistant, heat-resistant, and water-resistant properties. However, water-based matte inks are preferred for their eco-friendliness and low odor during printing processes.
Polyethylene Shrink Film (Proven durability for long-lasting vibrancy)
For polyethylene shrink film applications in the packaging industry, the use of water-based inks ensures proven durability for long-lasting vibrancy without compromising on print quality or color vibrancy. Solvent-based inks may offer similar performance but with higher VOC emissions.
Aluminum foil, surface printing with aluminum coating
When surface printing on aluminum foil with an aluminum coating is required for packaging materials such as food packaging or pharmaceutical products, both water-based and solvent-based inks can deliver exceptional adhesion and print quality. However, water-based inks are often favored for their lower environmental impact and safer handling.
Print Quality and Color Vibrancy
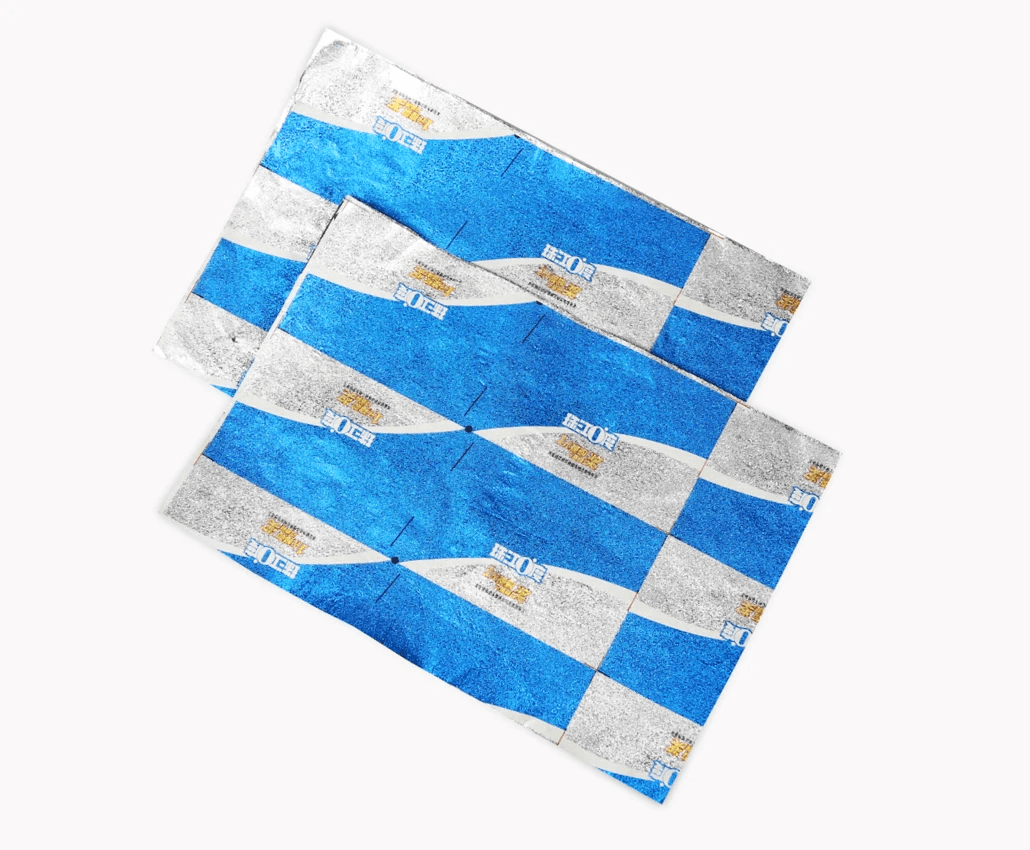
When comparing Water Based Ink V.S Solvent Based Ink, color accuracy and vibrancy are crucial factors to consider. Water-based inks are known for their ability to deliver vibrant and accurate colors, making them ideal for high-quality printing projects. On the other hand, solvent-based inks may sometimes struggle to achieve the same level of color accuracy and vibrancy due to their chemical composition.
Color accuracy and vibrancy
Water-based inks offer exceptional color accuracy and vibrancy, providing a wide range of vivid hues that remain true to the original artwork. This makes them an excellent choice for packaging inks, especially when precise color matching is essential for branding consistency across various products. In contrast, solvent-based inks may exhibit slight variations in color due to their chemical properties, potentially impacting the overall print quality.
Longevity and resistance to fading
In terms of longevity and resistance to fading, water-based inks have proven to outperform solvent-based inks. Their formulation allows for better adhesion to substrates, resulting in prints that maintain their vibrancy over time without succumbing to fading or discoloration. This is particularly important for packaging ink applications where durability is paramount, ensuring that the final product maintains its visual appeal throughout its shelf life.
Impact on packaging aesthetics
The choice between water-based ink, solvent ink, or UV ink can significantly impact packaging aesthetics. Water-based inks are renowned for producing sharp and vibrant prints that enhance the visual appeal of packaging materials, creating a lasting impression on consumers. In contrast, solvent-based inks may sometimes fall short when it comes to achieving the same level of aesthetic impact due to potential color inconsistencies and reduced vibrancy.
By carefully considering the print quality and color vibrancy offered by different types of inks such as water based ink v.s solvent based ink , businesses can make informed decisions that elevate their branding efforts while ensuring long-lasting visual impact on consumers.
Versatility and Suitability
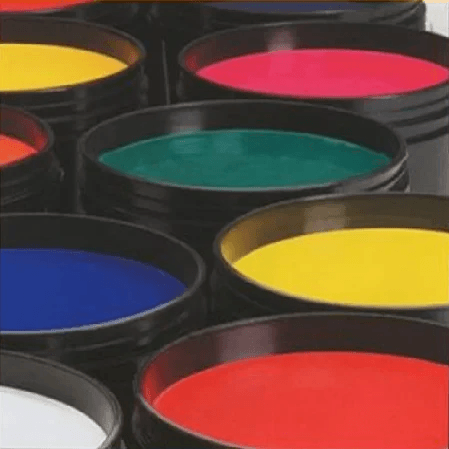
When it comes to versatility and suitability, Water Based Ink V.S Solvent Based Ink has a clear winner. Water-based ink offers excellent compatibility with different substrates such as paper, cardboard, and various plastics, making it a versatile choice for packaging inks. On the other hand, solvent ink may have limitations in terms of substrate compatibility, especially with certain types of plastics.
Compatibility with different substrates
Water-based ink demonstrates exceptional flexibility in printing techniques and processes, allowing for seamless adaptation to various printing requirements. Its ability to adhere to a wide range of substrates ensures that it can meet the diverse needs of the packaging industry. In contrast, solvent ink may require specific printing techniques and processes that are not as adaptable to different packaging materials.
Flexibility in printing techniques and processes
In the competitive packaging ink market, adaptability to various packaging requirements is crucial for success. Water-based ink offers the advantage of being able to meet a wide range of packaging needs, from food packaging to industrial applications. Its versatility makes it an ideal choice for businesses seeking cost-effective solutions without compromising on quality or performance.
Cost and Efficiency
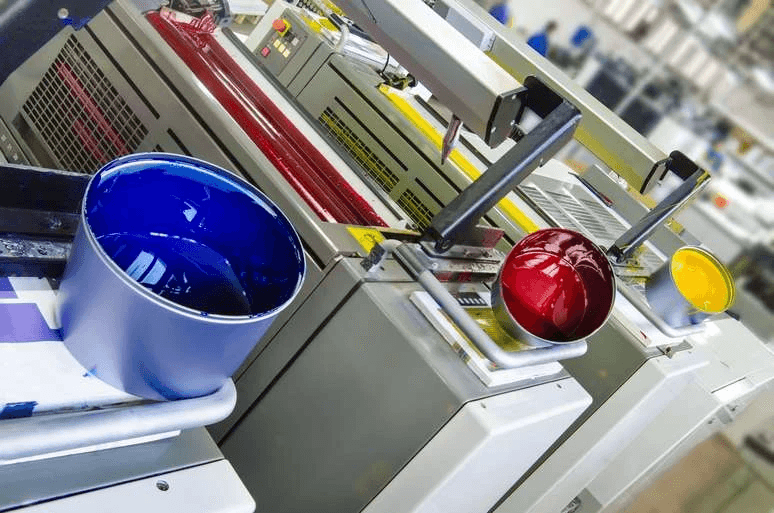
When it comes to the initial investment and operational expenses, water-based ink tends to have a higher upfront cost due to the need for specialized equipment and thorough drying processes. On the other hand, solvent-based ink may require less initial investment but can lead to higher operational expenses due to the need for ventilation and air pollution control measures.
Initial investment and operational expenses
Water-based ink typically requires specialized equipment such as high-quality anilox rollers and efficient drying systems, leading to a higher initial investment. Additionally, the need for thorough drying processes can increase operational expenses in terms of energy consumption. Conversely, solvent-based ink may have lower initial investment requirements but can lead to higher operational expenses due to the need for ventilation systems and air pollution control measures.
Additionally, the production speed of water-based ink can be slower compared to solvent-based ink, as the drying process takes longer. This can impact overall productivity and output, potentially leading to higher labor costs and longer lead times for fulfilling orders. On the other hand, solvent-based ink typically dries faster, allowing for quicker production speeds and potentially lower labor costs.
Production speed and drying time
In terms of production speed and drying time, water-based ink may require longer drying times compared to solvent-based ink, which can impact overall production efficiency. However, advancements in technology have led to improved drying systems for water-based inks, reducing the gap in production speed between water-based and solvent-based options.
Additionally, water-based inks are generally more cost-effective than solvent-based inks, as they require fewer harmful chemicals and additives. This can lead to a higher return on investment for businesses that choose to switch to water-based options. With the increasing focus on sustainability and environmental responsibility, the cost-effectiveness of water-based inks is becoming an attractive factor for many companies looking to improve their bottom line while reducing their carbon footprint.
Overall cost-effectiveness and ROI
When considering overall cost-effectiveness and return on investment (ROI), it's essential to weigh the initial investment and operational expenses against long-term benefits such as reduced environmental impact and enhanced safety measures associated with water-based ink. Additionally, factors such as improved print quality, color vibrancy, and longevity can contribute significantly to the overall cost-effectiveness of using water-based ink over solvent-based options.
Furthermore, water-based ink offers the advantage of being more versatile and compatible with a wider range of substrates, including paper, cardboard, and fabric. This versatility can lead to cost savings by eliminating the need for multiple types of ink for different materials, streamlining production processes, and reducing waste. In addition, the ability to achieve sharper details and finer lines with water-based ink can result in cost savings by minimizing rework and improving overall efficiency in the printing process.
Conclusion
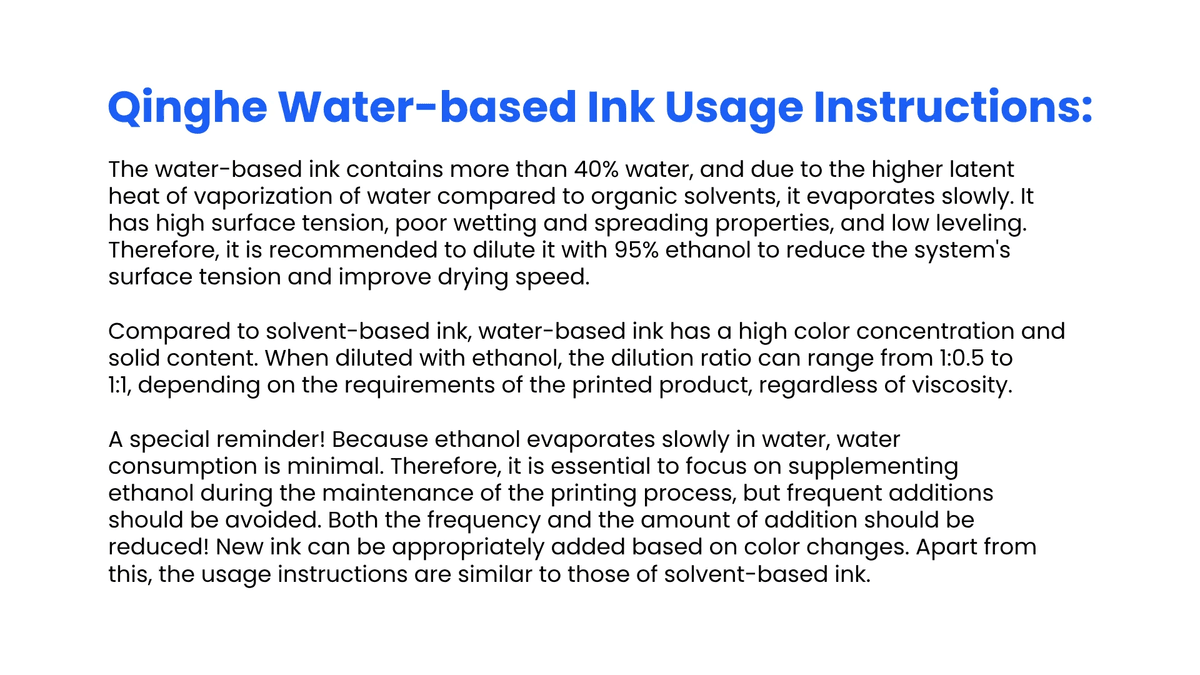
In conclusion, when it comes to choosing between water-based ink and solvent-based ink, it's crucial to make informed decisions for your printing projects. Consider the perfect balance between quality and efficiency to ensure the best results for your packaging inks. Navigating the water-based ink V.S solvent-based ink dilemma requires careful evaluation of factors such as print quality, color vibrancy, versatility, suitability, cost, and efficiency.
Making Informed Decisions for Your Printing Projects
When selecting packaging inks and coatings for your printing projects, take into account the specific requirements of your materials and the desired end result. Understanding the differences between water-based ink, solvent ink, and UV ink will help you make informed decisions that align with your printing needs.
Finding the Perfect Balance for Quality and Efficiency
Finding the perfect balance between quality and efficiency is essential when choosing between water-based ink V.S solvent-based ink. Consider factors such as print quality, color vibrancy, longevity, compatibility with different substrates, flexibility in printing techniques and processes, as well as overall cost-effectiveness.
Navigating the Water Based Ink V.S Solvent Based Ink Dilemma
Navigating the water-based ink V.S solvent-based ink dilemma involves carefully weighing the pros and cons of each type of ink based on your specific requirements. Whether you prioritize environmental impact, safety considerations, print quality or cost-effectiveness - understanding these key factors will guide you towards making an informed decision that aligns with your printing goals.