Introduction
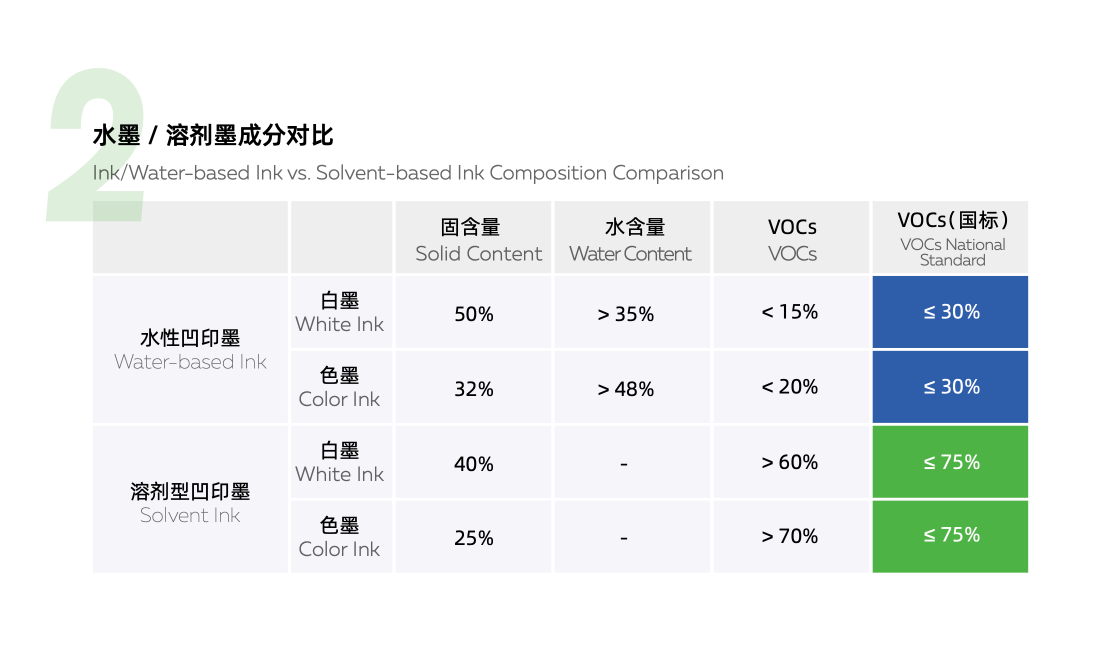
Understanding the viscosity of ink is crucial for producing high-quality prints. Ink's viscosity refers to its resistance to flow, and controlling it is essential for achieving optimal print results. At Qinghe Chemical, we are committed to providing top-notch quality inks that meet the highest standards of viscosity management.
Understanding the Viscosity of Ink
The viscosity of ink refers to its thickness or resistance to flow, which directly impacts its performance during the printing process. Low viscosity means the ink flows more easily, improving color consistency and faster drying times.
Controlling the viscosity of ink is crucial for ensuring that it performs optimally during the printing process. By maintaining the right viscosity, printers can achieve consistent color quality and prevent smudging or bleeding. Additionally, controlling viscosity allows for better control over ink coverage and adhesion to various substrates, resulting in high-quality printed materials that meet industry standards.
Importance of Controlling Viscosity
Maintaining consistent ink viscosity is essential for achieving exceptional printing results. Here's why it matters:
- Consistent Print Quality: Proper viscosity ensures the ink lays down evenly, creating crisp and clear images on any project.
- Performance Across Processes: Qinghe Chemical's inks perform flawlessly across different printing methods, from offset to inkjet.
- Reduced Maintenance: Optimal viscosity minimizes print head clogging and other issues, reducing maintenance downtime.
- Optimal Density for Every Application: Whether you need bold colors or subtle gradients, controlled viscosity delivers the perfect density.
By meticulously controlling viscosity, Qinghe Chemical guarantees its inks flow flawlessly for superior printing on any substrate. This commitment to detail ensures you consistently achieve the highest quality results, regardless of your printing needs.
Qinghe Chemical's Commitment to Quality
At Qinghe Chemical, we are dedicated to providing inks with precisely controlled viscosities that deliver exceptional print results every time. Our expertise in viscosity management allows us to offer innovative solutions that take print quality to the next level. By continuously investing in research and development, we ensure that our inks meet the evolving needs of the printing industry, keeping our customers ahead of the curve. Additionally, our commitment to quality extends to our environmentally friendly production processes, ensuring that our inks perform exceptionally and minimize their impact on the planet.
What is
the Viscosity of Ink?
Viscosity refers to ink's resistance to flow, and it plays a crucial role in the printing process. Low viscosity means the ink flows more easily, resulting in smoother and more consistent print quality. Adjusting viscosity for different printing processes is essential for achieving optimal results.
Definition and Importance
The viscosity of ink measures its internal friction, determining how easily it flows. Low-viscosity ink has a thinner consistency, allowing it to spread more evenly on the printing substrate. This is crucial for achieving vibrant and uniform colors in the final printed product.
Low-viscosity ink also helps to prevent clogging in the printing equipment, ensuring a smooth and uninterrupted printing process. This is particularly important for high-speed printing operations, where interruptions can lead to costly downtime and production delays. Additionally, the ability of low-viscosity ink to flow smoothly through the nozzles of the printing equipment results in sharper and more precise printed images, enhancing overall print quality.
Effects on Print Quality
Ink viscosity, a measure of an ink's thickness, is critical in determining the quality of your prints. Here's how low-viscosity inks can significantly improve your printing results:
- Enhanced Color Saturation: Low-viscosity inks flow more freely, allowing for a more even distribution of ink pigments on the paper. This results in richer, more vibrant colors in your prints.
- Sharper Image Details: The finer consistency of low-viscosity inks enables printers to produce sharper dots, leading to crisper lines and finer details in your images.
- Reduced Smudging and Bleeding: Since low-viscosity inks dry faster, there's less chance of them smudging or bleeding into each other during printing. This ensures cleaner and more professional-looking prints.
Using low-viscosity inks, you can achieve superior print quality with richer colors, sharper details, and a cleaner finish.
Adjusting Viscosity for Different Printing Processes
Different printing processes require varying levels of ink viscosity for optimal results. For example, offset printing typically requires lower viscosity inks to achieve precise color registration and smooth coverage on the substrate. On the other hand, screen printing may benefit from slightly higher viscosity to prevent excessive spreading on porous materials.
In addition to offset and screen printing, flexographic printing requires specific ink viscosities to ensure high-quality results. Flexographic printing, commonly used for packaging materials, benefits from inks with medium viscosity to achieve precise and consistent coverage on various substrates. By adjusting the viscosity of the ink to suit the unique requirements of each printing process, printers can minimize issues such as smudging, bleeding, and poor adhesion, ultimately improving the overall print quality.
Benefits of Low Viscosity
Low-viscosity inks offer myriad benefits that can significantly improve the quality of your prints. Firstly, they provide improved color consistency by ensuring the ink spreads evenly and smoothly across the substrate, resulting in vibrant and uniform hues throughout your designs. This means no more patchy or streaky prints, giving you the confidence that your final product will always look flawless.
Improved Color Consistency
Low-viscosity inks promote improved color consistency by ensuring an even smooth ink spread for vibrant and uniform hues.
Faster Drying Times
Additionally, low-viscosity inks boast faster drying times and are a game-changer for any printing operation. This means reduced waiting times between printing and finishing processes, allowing you to increase productivity and meet tight deadlines without compromising on quality.
Reduced Maintenance Requirements
Moreover, low-viscosity inks can help reduce maintenance requirements for your printing equipment. Their smoother flow properties minimize clogging and build-up within the machinery, leading to less downtime for cleaning and maintenance, ultimately saving you time and money.
Methods for Controlling Viscosity
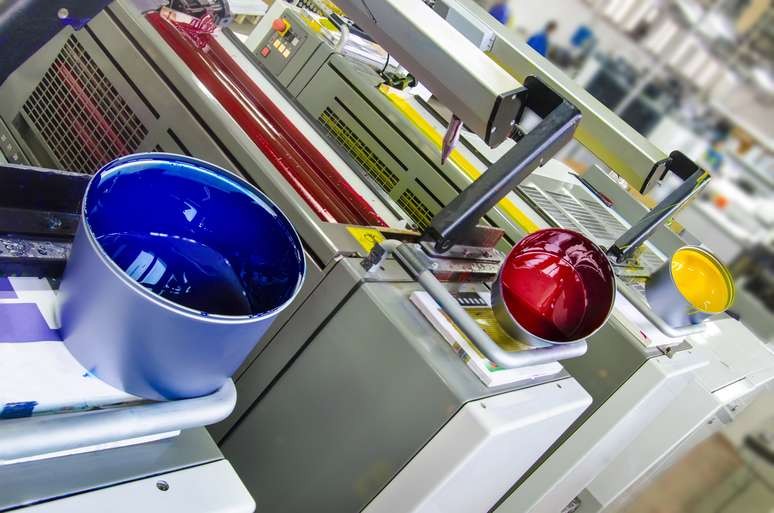
Several effective methods can be employed when it comes to managing the viscosity of ink. One common approach is to add solvents or thinners to the ink, which helps to reduce its viscosity and improve flow. This method is particularly useful when dealing with high-viscosity inks that must be thinned out for specific printing processes. Another method involves using rheology modifiers, which can alter the ink's flow behavior and help achieve the desired viscosity. Lastly, temperature control can also be crucial in managing ink viscosity, as heating or cooling the ink can effectively adjust its flow properties.
Adding Solvents or Thinners
Adding solvents or thinners to ink is a tried-and-true method for reducing viscosity and improving printability. Incorporating these substances into the ink formulation makes achieving the desired consistency and flow behavior easier for optimal printing results. Whether adjusting the viscosity for different substrates or accommodating various printing processes, adding solvents or thinners offers a versatile solution for controlling ink viscosity.
Using Rheology Modifiers
Rheology modifiers are essential tools for fine-tuning the flow properties of ink and achieving low-viscosity formulations. These additives can help enhance printability by adjusting the rheological characteristics of the ink, ensuring smooth and consistent application on different surfaces. By utilizing rheology modifiers, printers can effectively tailor the viscosity of their inks to meet specific requirements and deliver superior print quality.
Temperature Control
Temperature control is another effective method for managing ink viscosity, as it directly influences the flow behavior of the ink. By regulating the temperature of the ink during production and printing processes, printers can optimize its viscosity for better performance and print quality. Whether it involves heating to lower viscosity or cooling to increase it, temperature control offers a practical approach to achieving ideal flow properties in inks.
Controlling ink viscosity is crucial for optimal print quality and performance. By employing these methods effectively, you can ensure that your inks have low viscosity when needed while maintaining excellent color consistency and print clarity throughout your production processes!
Impact of Viscosity on Density of Ink
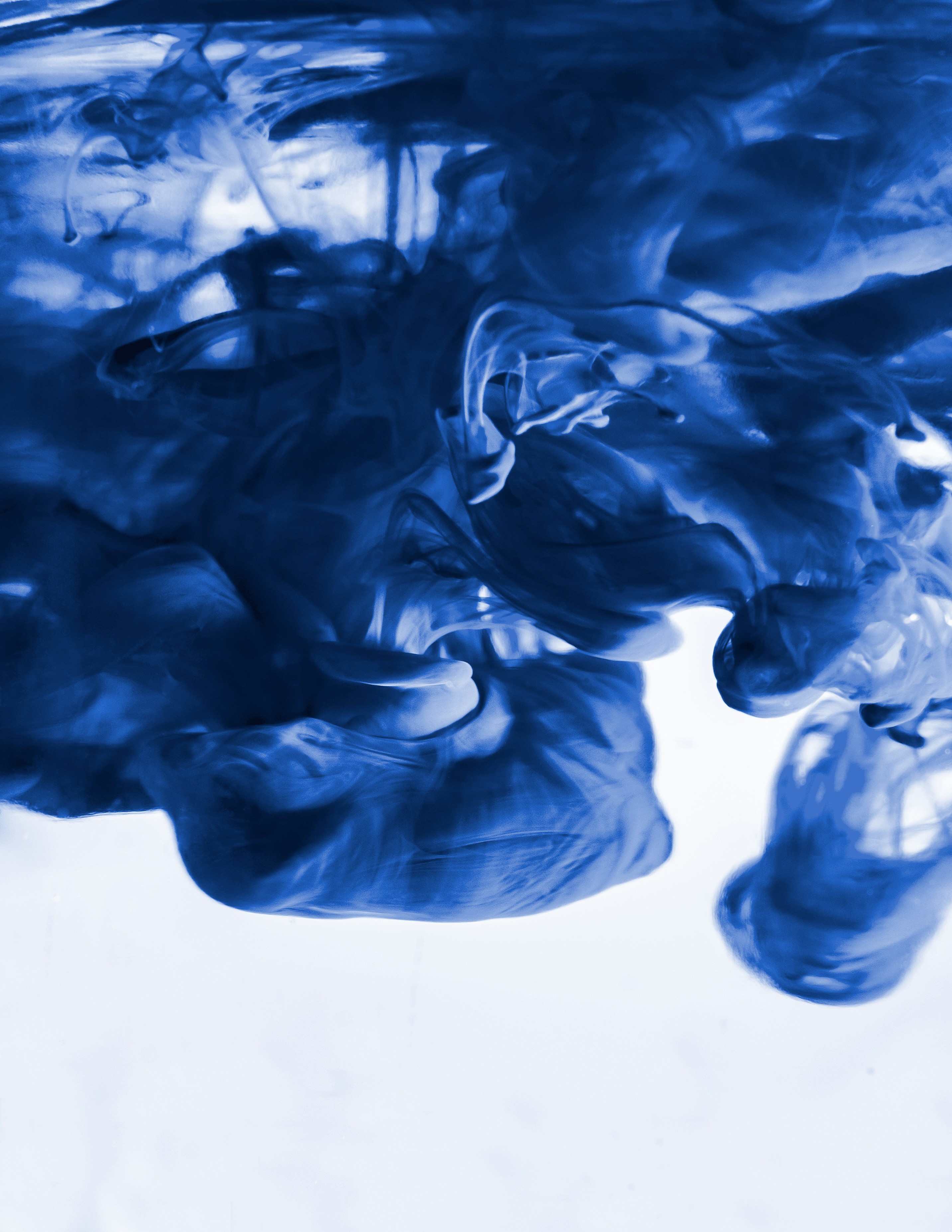
The viscosity of ink plays a crucial role in determining its density, which refers to the concentration of the ink's pigments and binders. Low-viscosity inks typically have a lower density due to their thinner consistency, allowing for smoother flow and better coverage on the printing substrate.
Relationship between Viscosity and Density
Ink viscosity and density are closely related properties affecting ink performance during printing. Here's a breakdown of how viscosity impacts density:
- Solvent Content: Low-viscosity inks typically contain more solvent. Solvents are thin liquids that help dissolve and disperse the ink's pigments and binders. Since solvents have low density, a higher solvent content leads to a less dense ink.
- Pigment Concentration: Pigments are the coloring agents in ink and tend to be denser than ink binders and solvents. Therefore, inks with a higher concentration of pigments will have a greater density. Low-viscosity inks often have a lower pigment concentration to maintain their flow properties.
- Binder Concentration: Binders act as adhesives to hold the ink particles together and adhere them to the printing surface. They also contribute to the ink's viscosity and density. Like pigments, binders tend to be denser than solvents. Consequently, low-viscosity inks may contain less binder to achieve a thinner consistency, reducing the overall density.
Understanding the relationship between viscosity and density is crucial for selecting the appropriate ink for your printing needs. Different printing methods require inks with specific viscosity and density ranges. By considering these factors, you can ensure optimal print quality and performance.
Influence on Ink Saturation and Print Clarity
The density of ink directly impacts its ability to saturate the printing substrate and achieve optimal print clarity. Low-viscosity ink with lower density can penetrate the substrate more effectively, producing vibrant colors and sharper details. This makes them ideal for high-quality prints with excellent color saturation and clarity.
Achieving Optimal Density for Different Substrates
Controlling the viscosity of ink is essential for achieving optimal density across different substrates. Low-viscosity inks can be adjusted to ensure consistent coverage and saturation on various materials, from paper to plastics. This versatility makes them preferred for printers seeking superior print quality across different applications.
By understanding the impact of viscosity on ink density, printers can make informed decisions about their ink choices to achieve superior print quality across various substrates. With low-viscosity inks offering enhanced color saturation and print clarity, it's clear that controlling viscosity is key to unlocking exceptional printing results.
Advantages of Low-Viscosity Inks
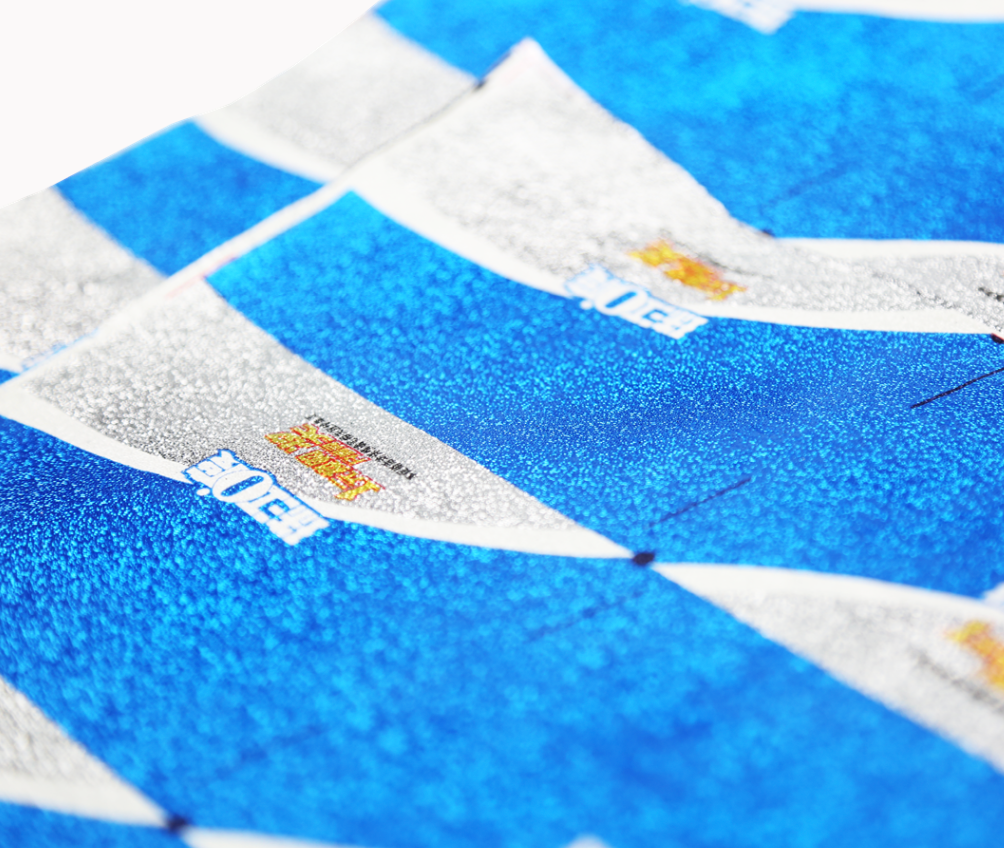
Low-viscosity inks offer a myriad of benefits that can significantly enhance print quality. One key advantage is the enhanced dot reproduction, which produces sharper and more precise images on the printed material. This is especially important for high-resolution graphics and detailed designs, as low-viscosity inks allow for better ink flow and coverage.
Enhanced Dot Reproduction
Low-viscosity inks enable printers to achieve better print uniformity, ensuring that colors are consistent throughout printing. This means there are no variations or discrepancies in color saturation, resulting in a more professional and polished final product. Additionally, low-viscosity inks help to minimize issues such as streaking or smudging, leading to a cleaner and more visually appealing output.
Better Print Uniformity
Qinghe Chemical has been at the forefront of developing innovative solutions for low-viscosity inks, utilizing advanced formulations and cutting-edge technology to meet the evolving needs of the printing industry. By leveraging our expertise in viscosity management, we have created inks that offer superior performance and contribute to increased operational efficiency and cost savings for our clients.
Qinghe Chemical's Innovative Solutions
At Qinghe Chemical, we understand viscosity's crucial role in achieving optimal print quality. That's why we have developed various innovative solutions to help our customers control and manage ink viscosity with precision. Our team of experts is constantly researching and developing new products and techniques to address the evolving needs of the printing industry, ensuring that our customers always have access to the latest advancements in viscosity management. Whether it's formulating low-viscosity inks for improved color consistency or providing guidance on adjusting viscosity for different printing processes, Qinghe Chemical is committed to delivering cutting-edge solutions that take print quality to the next level. With our innovative approach to viscosity management, you can trust Qinghe Chemical to be your partner in achieving print perfection.
Taking Your Print Quality to the Next Level
In conclusion, understanding the viscosity of ink is crucial for achieving impeccable print quality. By controlling viscosity, printers can ensure consistent color, faster drying times, and reduced maintenance requirements. With Qinghe Chemical's expertise in viscosity management, you can take your print quality to the next level and achieve print perfection.
Achieving Print Perfection with Controlled Viscosity
By mastering the viscosity of ink, printers can achieve print perfection by ensuring optimal color consistency, improved dot reproduction, and better print uniformity. Low-viscosity inks offer enhanced print quality, and Qinghe Chemical's commitment to quality ensures that you have access to the best solutions for achieving controlled viscosity.
By understanding the impact of viscosity on ink flow, printers can also minimize issues such as smudging and bleeding, resulting in cleaner and sharper prints. With Qinghe Chemical's expertise in viscosity management, printers can confidently achieve the desired print quality without compromising color vibrancy or image clarity. This control over ink viscosity ultimately leads to a more efficient printing process, reducing waste and improving overall productivity.
Qinghe Chemical's Expertise in Viscosity Management
Qinghe Chemical's dedication to providing innovative solutions for controlling ink viscosity sets them apart as industry leaders. Their expertise in developing low-viscosity inks allows printers to achieve superior results and take their printing capabilities to new heights. By offering a range of viscosity management options, Qinghe Chemical ensures that printers can customize their ink solutions to meet specific printing needs, whether for high-speed commercial printing or intricate, detailed designs. This level of flexibility and precision sets Qinghe Chemical apart from competitors, giving printers the confidence to tackle any project easily.
With Qinghe Chemical's range of low-viscosity inks and their commitment to quality control, you can elevate your print quality to new levels. By understanding the impact of viscosity on the density of ink and utilizing methods for controlling viscosity, you can ensure optimal print clarity and saturation on different substrates. In addition, Qinghe Chemical offers a wide selection of color options for their low-viscosity inks, allowing you to achieve vibrant and accurate color reproduction in your prints. This means that whether you're printing on paper, cardboard, or other materials, you can trust that your colors will pop and make a lasting impression.