Introduction
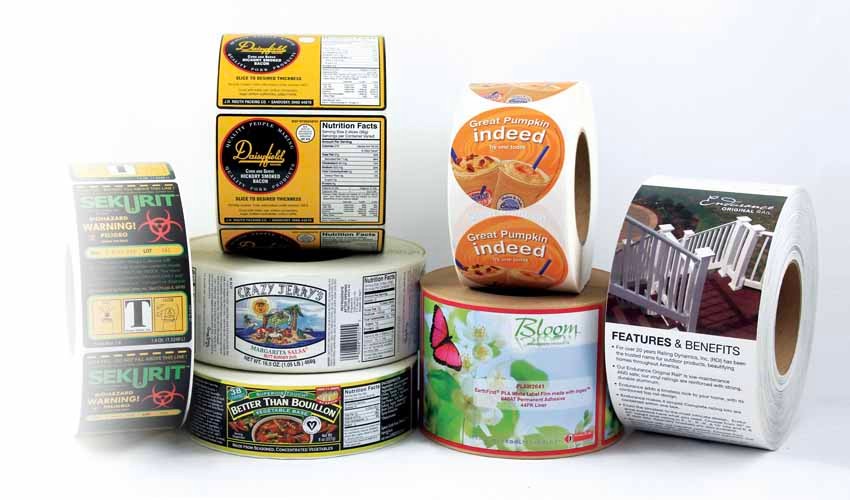
When it comes to printing on food packaging, using the right ink is crucial. Food grade ink ensures safety and compliance with regulations, making it an essential choice for food-related printing needs. In this guide, we will explore the definition, advantages, and applications of food grade ink.
Understanding Food Grade Ink
Food grade ink is specifically formulated to be safe for direct contact with food products. It meets stringent regulatory standards and is designed to prevent any harmful substances from leaching into the packaged food. This makes it a reliable choice for ensuring consumer safety and satisfaction.
Advantages of Using Food Grade Ink
The use of food grade ink offers several advantages, including environmental sustainability, health and safety benefits, as well as cost efficiency. With its ability to meet strict regulatory requirements while also being eco-friendly, it's a smart choice for conscious brands.
Applications of Food Grade Ink
Food grade ink finds wide-ranging applications in the food packaging industry, including flexible packaging, labeling and branding of food products, as well as direct printing on food items themselves. Its versatility makes it a valuable asset in ensuring the safety and quality of packaged foods.
What is Food Grade Ink?
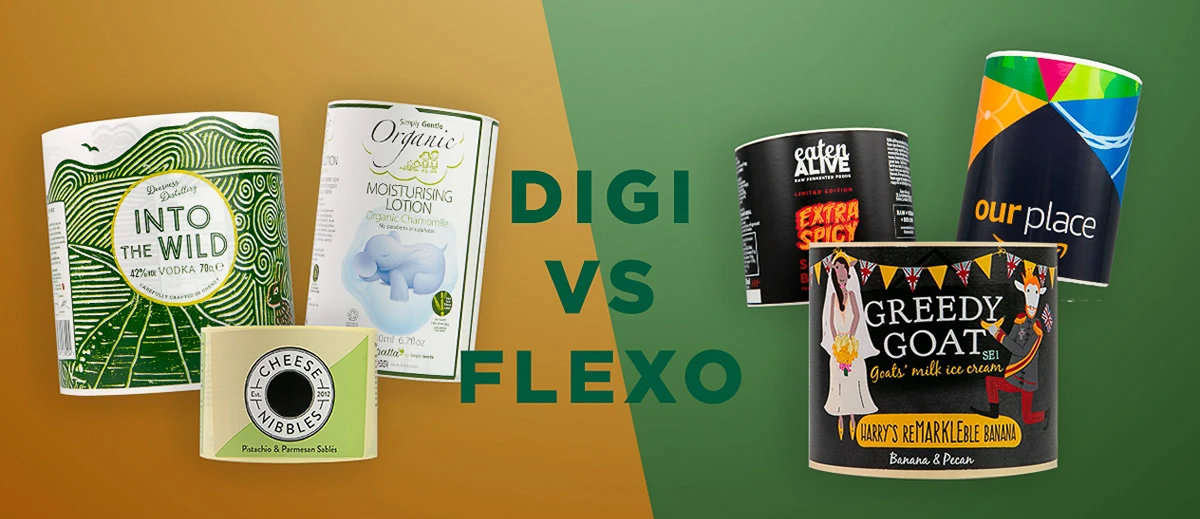
Food grade ink is a specialized type of ink that is safe for direct contact with food products. It is composed of non-toxic, food-grade materials that comply with strict regulatory standards to ensure safety and quality. This type of ink is designed to be versatile and compatible with various substrates commonly used in food packaging and labeling.
Definition and Composition
Food grade ink is formulated with ingredients that are specifically approved for use in printing on food packaging and labeling. These inks are typically free from heavy metals, mineral oils, and other harmful substances that could potentially contaminate food products. The composition of food grade ink ensures that it meets the stringent safety requirements for direct contact with consumable goods.
Regulatory Compliance and Safety Standards
Food grade ink must adhere to strict regulations set forth by organizations such as the FDA and the European Food Safety Authority (EFSA). These standards ensure that the ink does not pose any health risks when it comes into contact with food items. Compliance with these safety standards is essential to guarantee the integrity of printed materials used in the food industry.
Versatility and Compatibility with Substrates
One of the key characteristics of food grade ink is its ability to adhere to a wide range of substrates commonly used in food packaging, including paper, cardboard, plastic, and metal. This versatility allows for seamless printing on various packaging materials while maintaining high levels of safety and compliance.
In addition to its ability to adhere to various substrates, food grade ink also boasts compatibility with different printing methods, such as flexographic, gravure, and digital printing. This flexibility allows for efficient and high-quality printing on food packaging materials, ensuring that the necessary information and branding are clearly and accurately displayed. Whether it's a simple design or intricate artwork, food grade ink can deliver exceptional results across different printing processes.
Benefits of Using Food Grade Ink
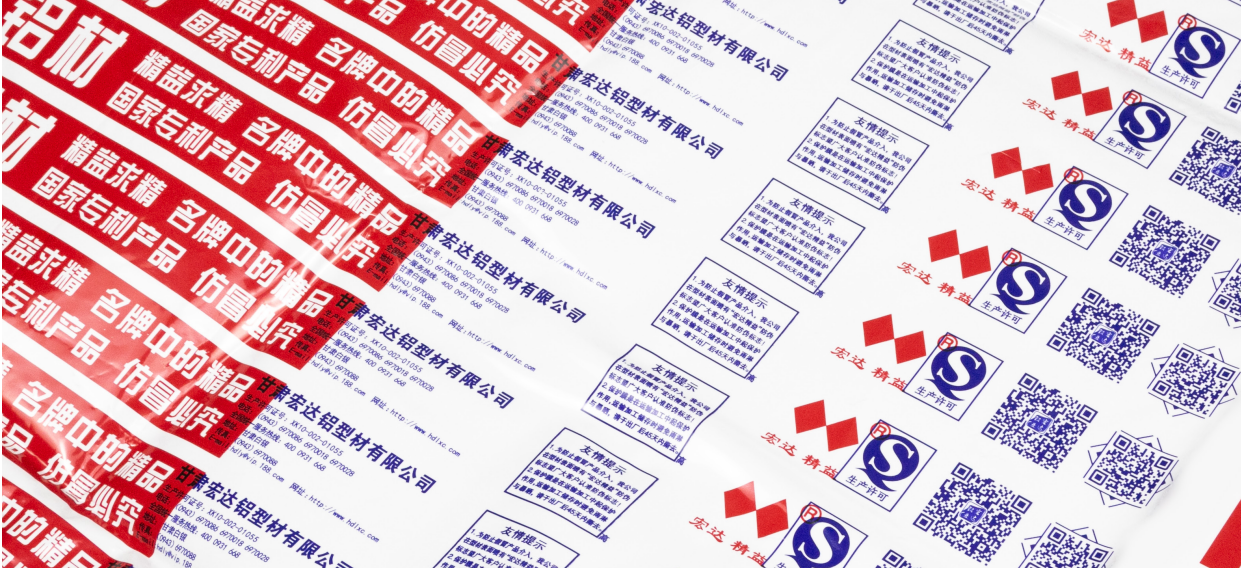
Environmental Sustainability
Food grade ink is a sustainable choice for printing needs, as it is typically made from natural, non-toxic ingredients that are safe for the environment. Its water-based composition reduces harmful emissions and minimizes the use of volatile organic compounds (VOCs), making it an eco-friendly option for packaging and labeling.
Health and Safety Benefits
One of the key advantages of using food grade ink is its non-toxic nature, which ensures that it does not pose any health risks when in contact with food products. This makes it a safe choice for flexible food packaging and direct food contact printing, providing consumers with peace of mind about the safety of their packaged goods.
Cost Efficiency and Viability
In addition to its environmental and health benefits, food grade ink also offers cost efficiency and viability for businesses. Its compatibility with various substrates allows for versatile applications, reducing the need for multiple types of ink. This streamlines production processes and ultimately leads to cost savings for manufacturers.
Applications of Food Grade Ink
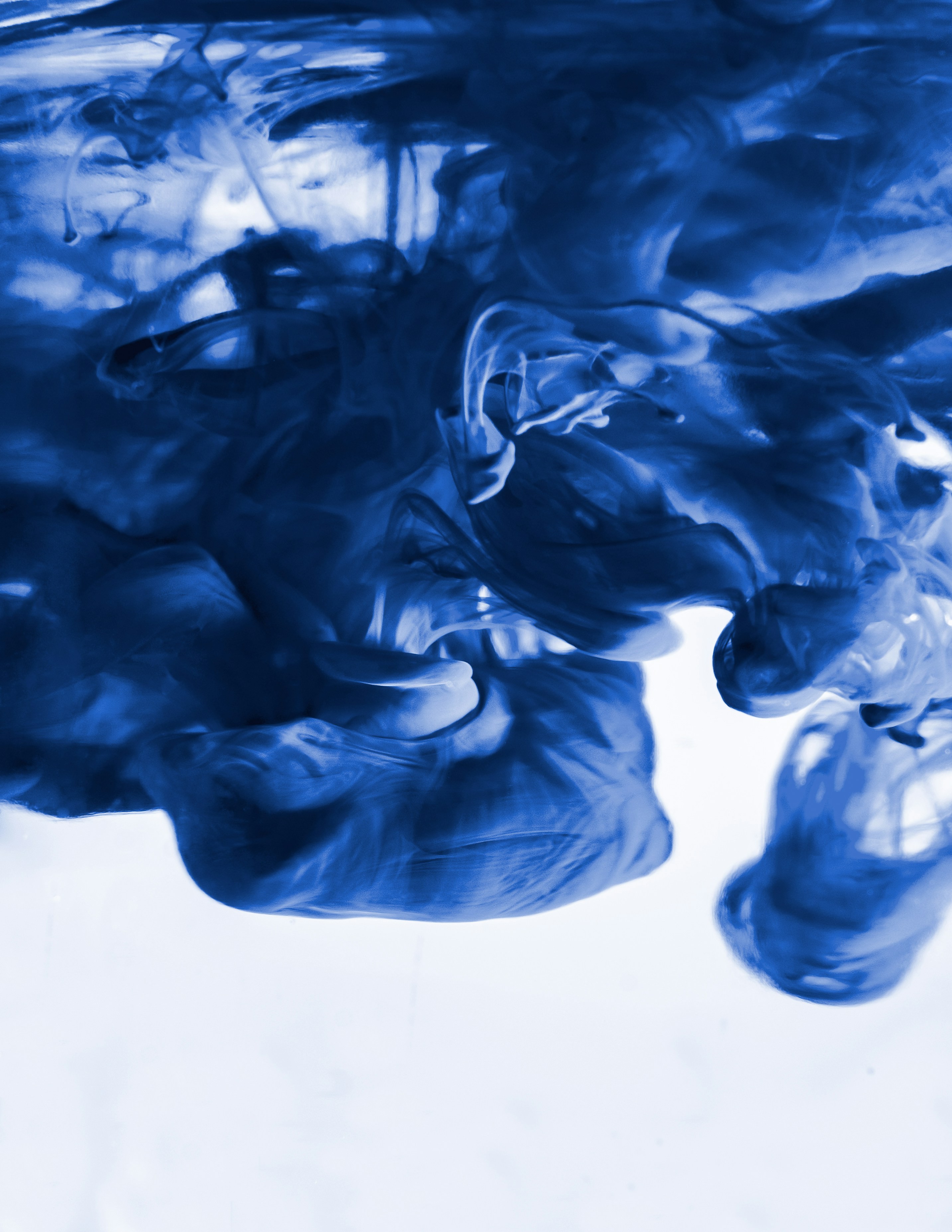
Flexible Food Packaging
Food grade ink is widely used in the printing of flexible food packaging, such as pouches, wrappers, and bags. Its ability to adhere to various substrates and maintain color vibrancy makes it an ideal choice for packaging that requires high-quality printing. Whether it's for snacks, frozen foods, or ready-to-eat meals, food grade ink ensures that the packaging is not only visually appealing but also safe for direct contact with food.
In addition to its visual appeal and safety for direct contact with food, food grade ink also offers the advantage of being resistant to moisture and grease. This is particularly important for flexible food packaging, as it ensures that the packaging maintains its integrity and does not compromise the quality of the printed design. Whether it's a pouch for granola bars or a wrapper for a sandwich, the durability of food grade ink contributes to the overall functionality of the packaging, providing a reliable solution for preserving and presenting various food products.
Food Labeling and Branding
When it comes to food labeling and branding, using food grade ink is crucial for ensuring that the information and imagery on the labels are safe for consumption. Whether it's nutritional information, ingredients lists, or eye-catching logos and designs, food grade ink provides a reliable solution for creating attractive and informative labels that comply with safety standards.
Food grade ink is specifically formulated to be non-toxic and safe for direct contact with food products, making it an essential component of food labeling and branding. In addition to safety considerations, food grade ink also offers excellent adhesion and durability, ensuring that labels remain intact and legible throughout the product's shelf life. This reliability is crucial for maintaining brand integrity and consumer trust, as it reflects a commitment to quality and attention to detail.
Direct Food Contact Printing
In industries where direct printing on food products is necessary, such as confectionery or fresh produce, water-based gravure and flexo printing inks are the go-to choice. These inks are formulated to meet strict regulations regarding direct contact with consumables while still delivering excellent print quality. From date coding to product identification, food grade ink plays a vital role in ensuring traceability and safety.
In addition to meeting regulatory standards, food grade inks are also designed to withstand the harsh conditions of food processing and packaging, such as exposure to moisture, heat, and cold. This ensures that the printed information remains clear and legible throughout the entire lifespan of the product, from production to consumption. Whether it's a best-before date or nutritional information, consumers rely on the accuracy and durability of direct food contact printing.
Water-Based Flexo Ink: The Ultimate Guide
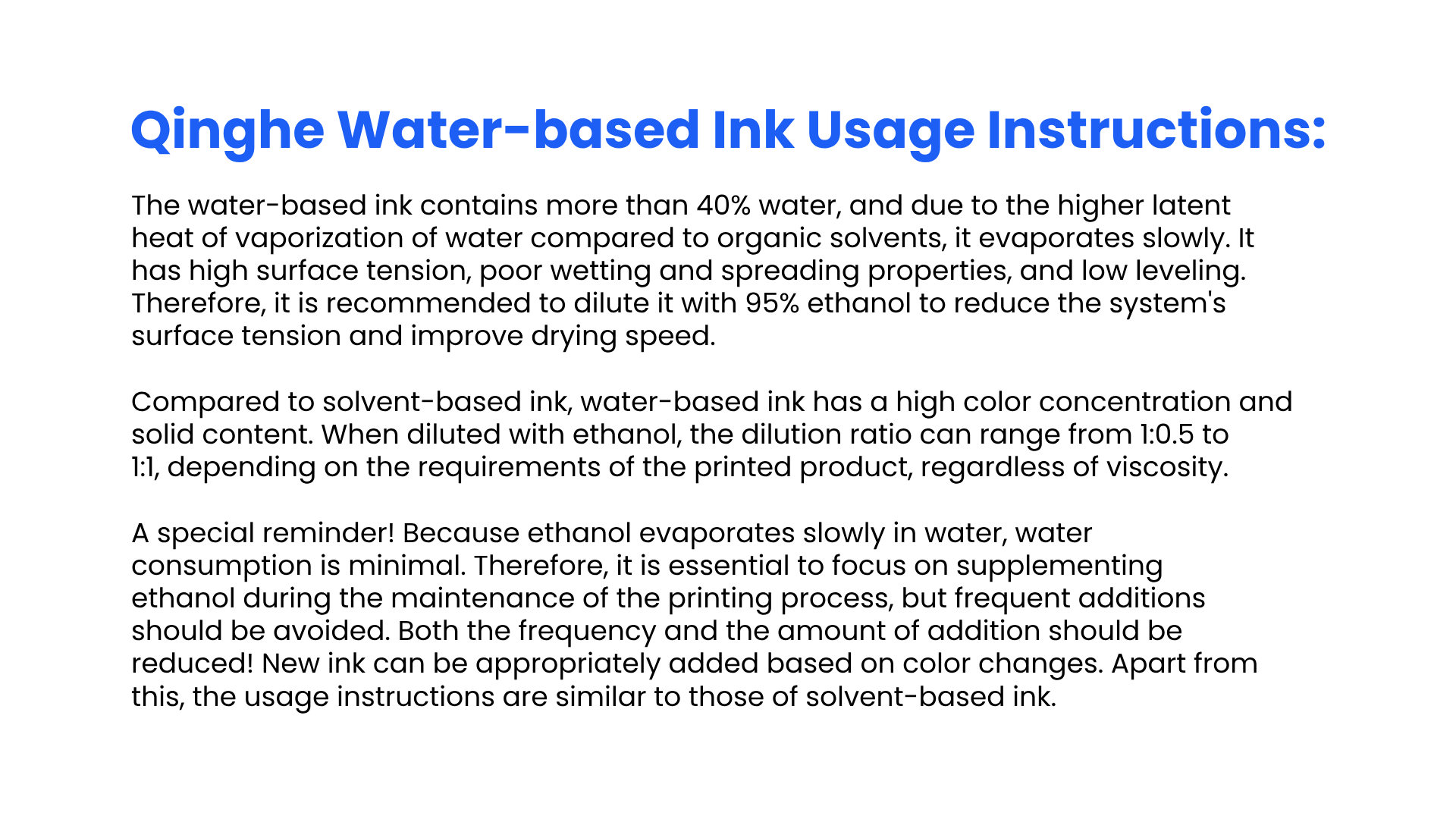
Properties and Characteristics
Water-based flexo ink is a type of food grade ink that is specifically designed for printing on food packaging materials. It is composed of water, colorants, binders, and additives, making it safe for direct contact with food products. The pH of water-based flexo ink typically ranges from 8 to 9, ensuring compatibility with various substrates while maintaining regulatory compliance.
Water-based flexo ink offers excellent printability and adhesion, making it ideal for high-speed printing processes commonly used in the food packaging industry. Its fast-drying properties help to increase production efficiency while reducing the risk of smudging or smearing during handling. Additionally, the water-based nature of this ink makes it easy to clean and maintain printing equipment, minimizing downtime and maintenance costs.
Printing Process and Techniques
The printing process using water-based flexo ink involves transferring the ink onto a substrate using flexible relief plates. This method allows for high-speed printing with excellent color reproduction and adhesion to different types of packaging materials. Water-based flexo inks are known for their fast drying time and low odor, making them ideal for use in food packaging applications.
Furthermore, water-based flexo inks are environmentally friendly, as they contain fewer volatile organic compounds (VOCs) compared to solvent-based inks. This makes them a more sustainable option for packaging printing, reducing the impact on the environment and improving workplace safety for operators. Additionally, the use of water-based flexo inks can result in cost savings for companies, as they require less clean-up and maintenance compared to other ink types, leading to increased efficiency and productivity.
Comparison with Other Ink Types
Compared to solvent-based or UV-curable inks, water-based flexo inks offer several advantages such as lower VOC emissions, reduced environmental impact, and improved safety for workers handling the ink. Additionally, water-based flexo inks provide vibrant colors and high print quality while meeting strict regulatory requirements for food contact materials.
Remember that when using water-based gravure and flexo printing inks, it's essential to consider the properties and characteristics of the ink as well as the printing process and techniques involved to ensure optimal results.
Drawbacks of Water-Based Flexo Ink
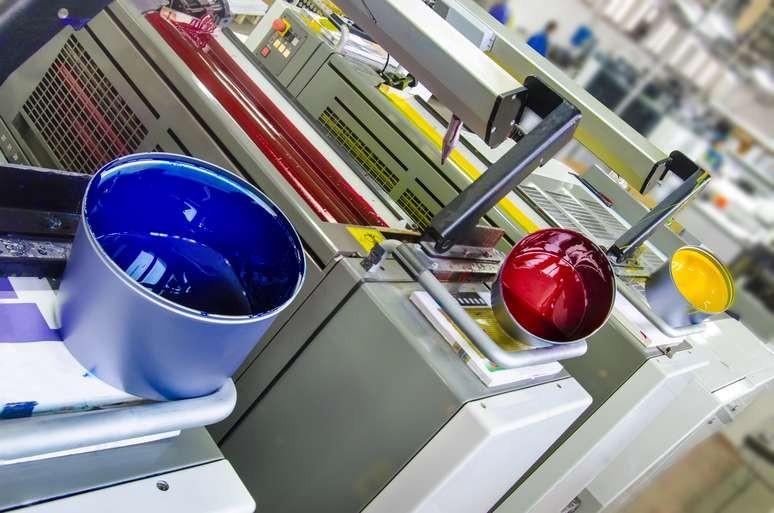
Limitations in Performance
One drawback of water-based flexo ink is its limitations in performance, particularly in terms of print quality and color vibrancy. Due to the nature of water-based ink, achieving intense and vivid colors can be challenging, leading to a lack of visual impact in printed materials.
Additionally, water-based flexo ink can present challenges in the printing process, as it may require specialized equipment and techniques to achieve satisfactory results. This can lead to increased production time and costs, as well as potential difficulties in matching colors and maintaining consistency across different print runs. These challenges can be a significant barrier for printers looking to meet the demands of clients who require high-quality, vibrant printed materials.
Challenges in Printing Process
Another drawback is the challenges it presents in the printing process. Water-based flexo ink requires careful handling and management during the printing process to ensure consistent and uniform application on various substrates. This can lead to increased production time and complexity.
Additionally, water-based flexo ink can be more prone to drying out or clogging in the printing equipment, requiring regular maintenance and cleaning to avoid disruptions in the production process. This adds another layer of complexity and potential downtime to the printing operation, impacting overall efficiency and output. Furthermore, the need for specialized training and expertise in handling water-based flexo ink adds to the challenges in the printing process, as operators must be well-versed in its unique properties and requirements to achieve optimal results.
Overcoming Potential Issues
Despite these drawbacks, potential issues with water-based flexo ink can be overcome with proper equipment, expertise, and quality control measures. By investing in advanced technology and skilled operators, it is possible to mitigate the limitations and challenges associated with this type of ink.
Food grade ink is an essential component for food packaging and labeling needs due to its safety standards and regulatory compliance requirements. When considering the use of water-based flexo ink for food-related applications, it's important to weigh its drawbacks against its benefits to make an informed decision that aligns with your printing needs.
Conclusion
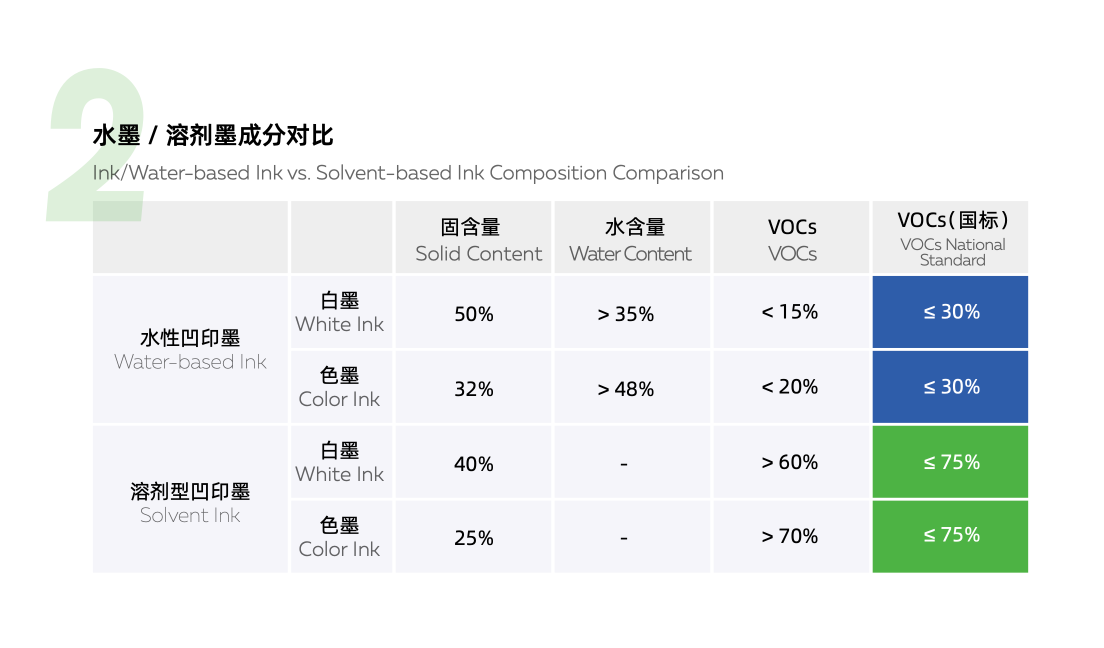
In conclusion, choosing the right food grade ink for your printing needs is crucial for ensuring safety and compliance with food packaging regulations. Embracing sustainability with water-based gravure and flexo printing inks can help reduce environmental impact while maintaining high-quality printing results. It's important to consider the drawbacks of flexography water-based ink, such as limitations in performance and challenges in the printing process, but these can be overcome with proper techniques and expertise.
Choosing the Right Food Grade Ink for Your Printing Needs
When selecting a food grade ink, consider factors such as regulatory compliance, substrate compatibility, and environmental sustainability. Water-based gravure and flexo printing inks offer a safe and versatile option for various food packaging applications, providing vibrant colors and excellent adhesion on different substrates.
Embracing Sustainability with Water-Based Gravure and Flexo Printing Inks
Water-based gravure and flexo printing inks are environmentally friendly options that reduce VOC emissions and minimize the use of hazardous chemicals. These inks are formulated with renewable resources and have low odor, making them ideal for sustainable packaging solutions that meet consumer demands for eco-friendly products.
Ensuring Safety and Compliance with Food Packaging Printing Needs
To ensure safety and compliance with food packaging printing needs, it's essential to use water-based gravure and flexo printing inks that adhere to strict regulatory standards. These inks have a neutral pH level, making them safe for direct food contact applications while delivering high-quality print results that meet industry requirements.