Introduction
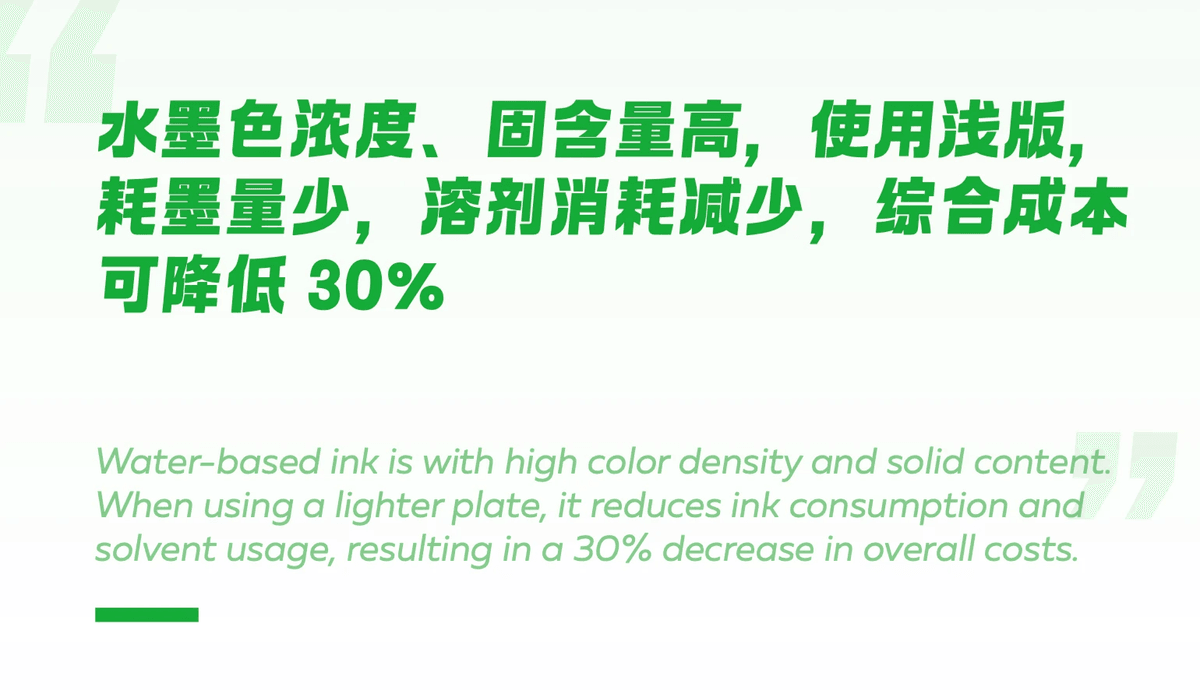
When it comes to printing on plastic, there are various methods and inks to consider. Understanding the basics of this process is essential for achieving high-quality results. Flexographic and gravure printing are two popular techniques used for plastic printing, each with its own unique advantages. Choosing the right ink is crucial for ensuring durability and vibrant colors in plastic prints.
The Basics of Printing on Plastic
Printing on plastic involves applying ink onto a plastic substrate to create labels, packaging, or other printed materials. The process requires specialized inks and printing techniques to ensure adhesion and longevity on the plastic surface.
Understanding Flexographic and Gravure Printing
Flexographic printing uses flexible relief plates to transfer ink onto the substrate, making it ideal for large volume runs and high-speed production. On the other hand, gravure printing utilizes engraved cylinders to apply ink, resulting in consistent and high-quality prints.
Flexographic printing is known for its ability to produce vibrant and eye-catching prints, making it a popular choice for packaging and labeling. Its flexibility allows for the use of a wide range of substrates, including paper, plastic, and cardboard, giving businesses the freedom to choose the most suitable material for their products. Additionally, the fast drying nature of flexographic inks makes them ideal for applications that require quick turnaround times, ensuring efficient and timely production.
Importance of Choosing the Right Ink
Selecting the appropriate ink is crucial for successful plastic printing. Flexographic ink manufacturers offer a wide range of options designed specifically for printing on plastics, while gravure inks are formulated to achieve precision and detail in prints. When choosing the right ink, it's essential to consider factors such as adhesion, durability, and color vibrancy. The wrong ink can result in smudging, fading, or poor adhesion to the plastic surface, leading to subpar print quality and wasted materials. Therefore, investing time and research into selecting the right ink can ultimately save time and resources in the long run.
Flexographic Printing on Plastic
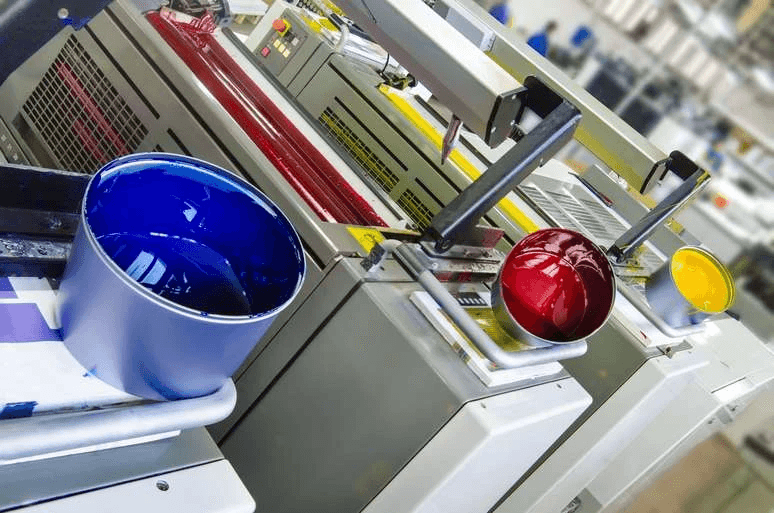
Flexographic printing on plastic offers a multitude of benefits, including high-speed production, cost-effectiveness, and the ability to print on a variety of substrates. The use of flexographic inks ensures vibrant and durable prints that are resistant to abrasion and fading, making them ideal for packaging and labeling applications.
Benefits of Flexographic Inks
Flexographic inks are formulated to adhere to a wide range of substrates, including plastic, paper, and film. These inks provide excellent color density and consistency, resulting in sharp and vibrant prints. Additionally, flexographic inks dry quickly, allowing for efficient production processes without compromising print quality.
Qinghe's Waterborne Polyurethane Inks
Qinghe's waterborne polyurethane inks are at the forefront of innovation in flexographic printing on plastic. These eco-friendly inks offer exceptional adhesion to various plastic substrates while minimizing environmental impact. With superior color retention and resistance to chemicals and moisture, Qinghe's waterborne polyurethane inks are the go-to choice for high-quality plastic printing.
Flexographic Ink Manufacturers
The market for flexographic ink manufacturers is vast, with numerous companies specializing in developing high-performance inks for plastic printing. Leading manufacturers such as Sun Chemical Corporation and Flint Group offer a wide range of flexographic inks tailored to meet the specific requirements of different plastic substrates.
Remember that when choosing a printing method for your plastic products or packaging materials, it's essential to consider the unique advantages offered by flexographic printing and the innovative solutions provided by industry leaders like Qinghe's waterborne polyurethane inks.
Gravure Printing on Plastic
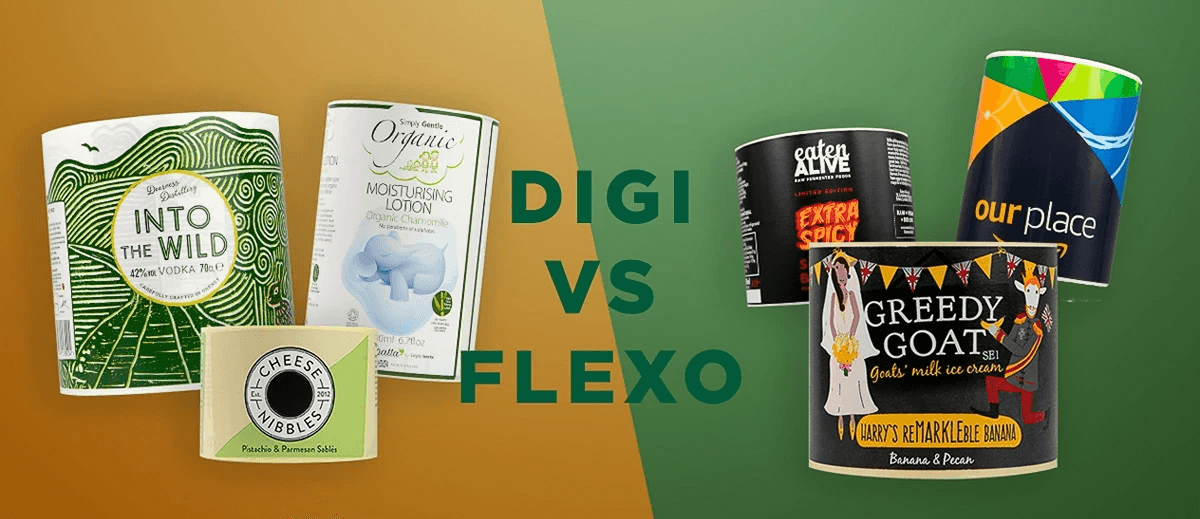
Gravure printing on plastic offers a high-quality, consistent print result, making it a popular choice for packaging and label printing. Gravure inks are specially formulated to adhere to plastic surfaces, ensuring vibrant colors and sharp details that stand out. The rotogravure printing inks industry continues to innovate, offering a wide range of options for different plastic materials and printing requirements.
Exploring Gravure Printing Inks
Gravure inks are designed to provide excellent adhesion to plastic substrates, ensuring durability and resistance to abrasion or moisture. These inks are formulated with specific properties that allow them to dry quickly and maintain their color intensity when printed on plastic surfaces. With a variety of formulations available, gravure printing inks can be tailored to meet the specific needs of different plastic materials and printing processes.
Achieving High-Quality Prints with Gravure
One of the key advantages of gravure printing on plastic is the ability to achieve high-quality prints with fine details and vibrant colors. The gravure process allows for precise ink transfer onto the plastic substrate, resulting in sharp images and consistent color reproduction. This makes gravure an ideal choice for applications where visual appeal is crucial, such as product packaging and labels.
In addition to its ability to produce high-quality prints, gravure printing on plastic also offers excellent durability. The ink used in gravure printing is typically formulated to adhere strongly to the plastic substrate, resulting in prints that are resistant to scratching, rubbing, and other forms of wear and tear. This makes gravure an ideal choice for applications where the printed material will be subjected to rough handling or harsh environmental conditions, ensuring that the visual appeal of the product packaging or labels remains intact throughout its lifespan.
The Rotogravure Printing Inks Industry
The rotogravure printing inks industry is constantly evolving to meet the demands of the market, offering advanced formulations that cater to different types of plastics and printing requirements. Manufacturers are developing new technologies and ink compositions that enhance print quality, adhesion, and durability on plastic substrates. As the demand for high-quality printed plastics grows, the rotogravure industry continues to push the boundaries of what is possible with ink technology.
Choosing the Right Plastic Material
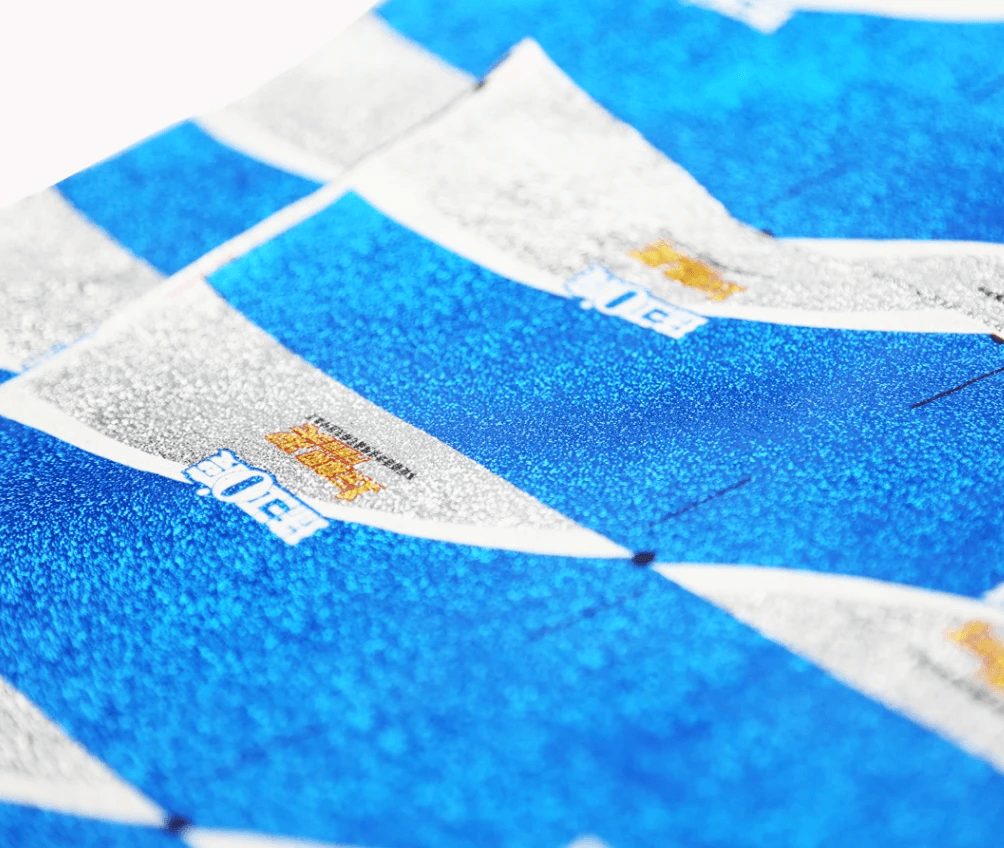
When considering PVC shrink film for printing on plastic, it's important to take into account its excellent printability and ability to conform to the shape of the product. PVC shrink film is commonly used for packaging products like CDs, DVDs, and software boxes due to its clarity and durability. It offers a high degree of printability, making it an ideal choice for flexographic and gravure printing on plastic.
Considerations for PVC Shrink Film
PVC shrink film is known for its ability to showcase vibrant colors and high-quality graphics when printed on. Its excellent dimensional stability ensures that the printed design remains intact even after the shrinking process. This makes it a popular choice for labeling and packaging applications where visual appeal is crucial. When using PVC shrink film for printing on plastic, it's essential to consider its compatibility with various ink types and printing methods.
Utilizing Matte Ink for Plastic
When aiming for a more sophisticated look in plastic printing, utilizing matte ink can create a unique aesthetic appeal. Matte ink adds a subtle texture to the surface of the plastic material, giving it a non-glossy finish that exudes elegance. This type of ink is commonly used in luxury product packaging, where a premium feel is desired. By carefully selecting the right ink type, you can achieve stunning results when printing on plastic with matte finishes.
When aiming for a more sophisticated look in plastic printing, utilizing matte ink can create a unique aesthetic appeal. Matte ink adds a subtle texture to the surface of the plastic material, giving it a non-glossy finish that exudes elegance. This type of ink is commonly used in luxury product packaging, where a premium feel is desired. By carefully selecting the right ink type, you can achieve stunning results when printing on plastic with matte finishes.
Durability of Polyethylene Shrink Film
Polyethylene shrink film offers exceptional durability when used for printing on plastic. Its resistance to tearing and puncturing makes it an ideal choice for products that require robust packaging solutions. The ability of polyethylene shrink film to withstand rough handling during transportation and storage ensures that the printed design remains intact throughout the entire product lifecycle.
Polyethylene shrink film not only offers exceptional durability, but it also provides a high level of protection against moisture, dust, and other environmental factors that could potentially damage the printed design. This makes it an ideal choice for products that need to maintain their visual appeal from the point of production to the point of sale. Additionally, the clarity and smooth surface of polyethylene shrink film ensure that the printed design stands out with vibrant colors and sharp details, enhancing the overall visual impact of the packaging.
Other Plastic Printing Options
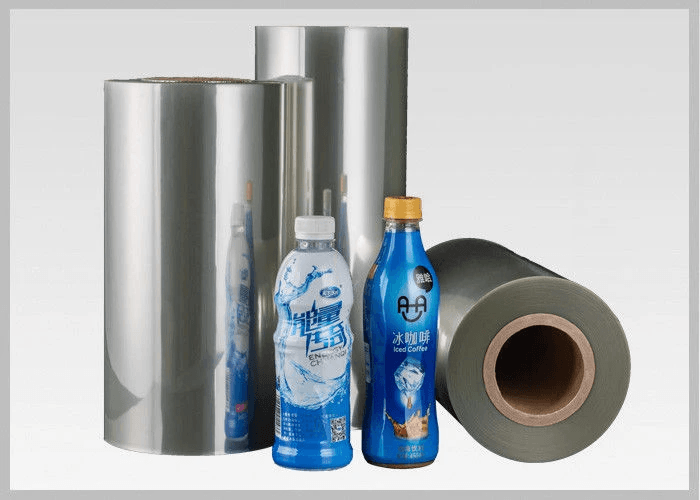
When it comes to printing on plastic, aluminum foil printing techniques offer a unique and eye-catching option. By using specialized inks and printing processes, aluminum foil can be used to create stunning designs and labels on plastic materials. This method is especially popular in the food and beverage industry for packaging that needs to stand out on the shelves.
Aluminum Foil Printing Techniques
Aluminum foil printing techniques involve transferring metallic pigments onto plastic surfaces using heat and pressure. This process creates a shiny, reflective effect that is both visually appealing and durable. The versatility of aluminum foil allows for intricate designs and vibrant colors, making it an ideal choice for high-end packaging and promotional materials.
Surface Printing with Aluminum Coating
Surface printing with aluminum coating is another innovative method for achieving striking visuals on plastic materials. By applying a thin layer of aluminum onto the surface of the plastic, printers can create a metallic sheen that enhances the overall appearance of the printed design. This technique is often used in cosmetic packaging and luxury product labeling.
Surface printing with aluminum coating is an effective way to add a touch of luxury and sophistication to plastic packaging. The metallic sheen created by the aluminum coating can elevate the perceived value of the product, making it more attractive to consumers. This method allows for endless design possibilities, from sleek and modern looks to timeless and elegant finishes.
Innovative Solutions for Plastic Printing Challenges
Innovative solutions for plastic printing challenges continue to emerge as technology advances. From specialized coatings to advanced application methods, printers are constantly finding new ways to overcome limitations in plastic printing. Whether it's improving adhesion, enhancing color vibrancy, or increasing durability, these innovations are shaping the future of plastic printing.
As technology advances, printers are constantly finding new ways to overcome limitations in plastic printing. One innovative solution that has emerged is the use of 3D printing technology to create complex and intricate designs on plastic surfaces. This allows for greater customization and personalization, opening up a world of possibilities for brand packaging and product design. Additionally, advancements in eco-friendly inks and materials are revolutionizing the industry, providing sustainable options for plastic printing that reduce environmental impact.
By incorporating aluminum foil printing techniques and surface printing with aluminum coating into your packaging designs, you can elevate your brand's visual appeal and make a lasting impression on consumers.
Conclusion
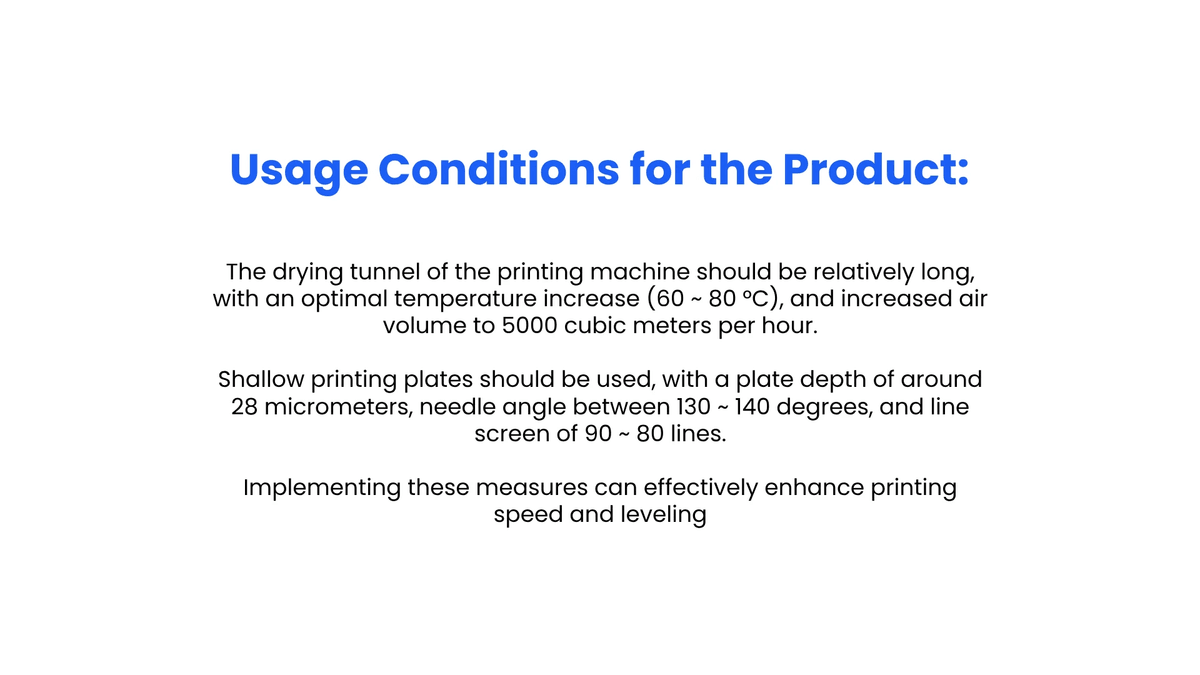
When it comes to printing on plastic, the best method for your needs depends on various factors such as the type of plastic, desired print quality, and budget. Flexographic printing offers versatility and cost-effectiveness, while gravure printing provides high-quality prints for larger volumes. With advancements in plastic printing technology, there are now innovative solutions available to address specific challenges in plastic printing. Qinghe's waterborne polyurethane inks stand out as a sustainable and high-performance option for both flexographic and gravure printing on plastic.
Choosing the Best Printing Method for Your Needs
Ultimately, choosing the best printing method for your needs requires careful consideration of your specific requirements. Flexographic ink manufacturers offer a wide range of options to suit different applications, while gravure ink is known for its ability to produce sharp and consistent prints. Understanding the advantages of each method will help you make an informed decision that aligns with your goals and budget.
Advancements in Plastic Printing Technology
Advancements in plastic printing technology have led to the development of specialized inks that can deliver exceptional results on various types of plastic materials. Whether it's achieving vibrant colors on PVC shrink film or enhancing durability with polyethylene shrink film, there are now more options available to meet specific needs. These advancements continue to push the boundaries of what is possible in plastic printing.
Qinghe's Waterborne Polyurethane Inks
Qinghe's waterborne polyurethane inks have gained recognition for their eco-friendly composition and outstanding performance in flexographic and gravure printing on plastic. These inks offer excellent adhesion, chemical resistance, and color retention, making them a top choice for brands looking to elevate their packaging with high-quality prints that also prioritize sustainability.