Introduction
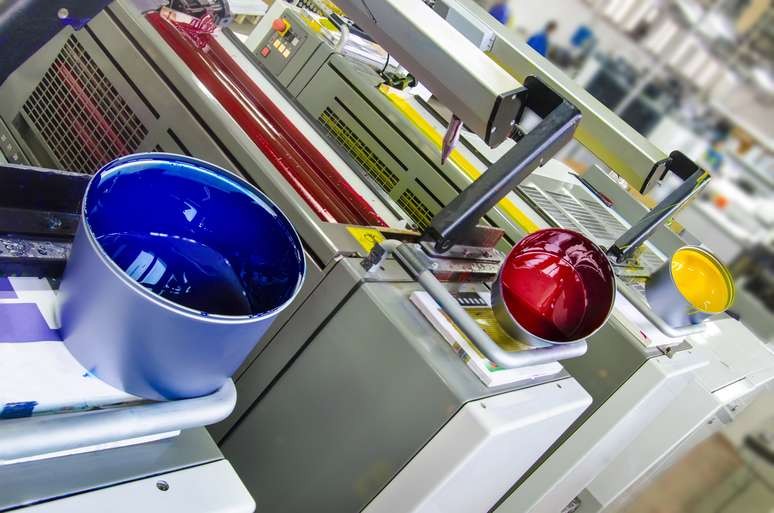
When it comes to plastic printing, the choice of ink is crucial for achieving high-quality results. With technological advancements, water-based ink has emerged as a game-changer, offering numerous benefits that traditional inks cannot match. As the demand for sustainable and eco-friendly solutions continues to grow, the importance of choosing the right ink for plastic printing has never been more significant. Innovations in plastic printing ink technology have paved the way for new possibilities and improved outcomes in the industry.
Benefits of Water-Based Ink for Plastic Printing
Water-based inks are gaining traction in plastic printing due to their numerous advantages. Here's why you should consider switching to water-based inks for your next plastic printing project:
- Enhanced Print Quality: Water-based inks, with their thinner consistency, are able to penetrate deeper into the plastic surface. This results in sharper prints with finer details and richer colors than traditional solvent-based inks.
- Environmentally Friendly: A key benefit of water-based inks is their eco-friendly nature. They contain minimal to no volatile organic compounds (VOCs) which are harmful air pollutants. Additionally, they are often petroleum-free, reducing reliance on fossil fuels.
- Safety and Regulation Compliance: Water-based inks pose minimal health risks to printers and users due to the lack of harsh chemicals. They also comply with stricter environmental regulations, making them a safe and responsible choice.
Water-based inks offer a compelling combination of superior print quality, environmental benefits, and safety considerations, making them a strong choice for the future of plastic printing.
Importance of Choosing the Right Ink for Plastic Printing
When it comes to plastic printing, selecting the right ink is vital for a successful outcome. The ink you choose will directly impact the print's adhesion, durability, and overall quality.
Here are some key factors to consider when choosing ink for plastic printing:
- Plastic Type: Different plastics have varying surface properties that affect ink adhesion. Matching the ink to the specific plastic type (e.g., PVC, PET) ensures optimal bonding for a long-lasting print.
- Desired Finish: Do you need a glossy, matte, or metallic finish? The ink formulation will determine the final aesthetic of your print.
- Environmental Exposure: Will the printed plastic be exposed to sunlight, chemicals, or extreme temperatures? Choose an ink formulated to withstand the anticipated environmental conditions.
- Printing Method: The printing method (e.g., screen printing, inkjet) will influence the compatible ink types.
By carefully considering these factors, you can select the right ink for your plastic printing project, guaranteeing vibrant and long-lasting results.
Innovations in Plastic Printing Ink Technology
Plastic printing ink technology's continuous evolution has led to remarkable performance and versatility advancements. Options such as plastisol ink, screen printing ink, and textile ink specifically formulated for use on plastics give printers access to a wide array of innovative solutions tailored to their specific needs. These innovations have opened up new opportunities and possibilities in plastic printing.
The advantages of water-based ink cannot be overlooked in plastic printing. Water-based inks offer a more environmentally friendly alternative to traditional solvent-based inks, reducing harmful emissions and promoting sustainability. Additionally, water-based inks provide excellent adhesion to various plastic substrates, ensuring high-quality and durable prints that meet industry standards. Furthermore, these inks offer a wider color gamut and better color consistency, allowing for more vibrant and precise prints on plastics.
The Advantages of Water-Based Ink
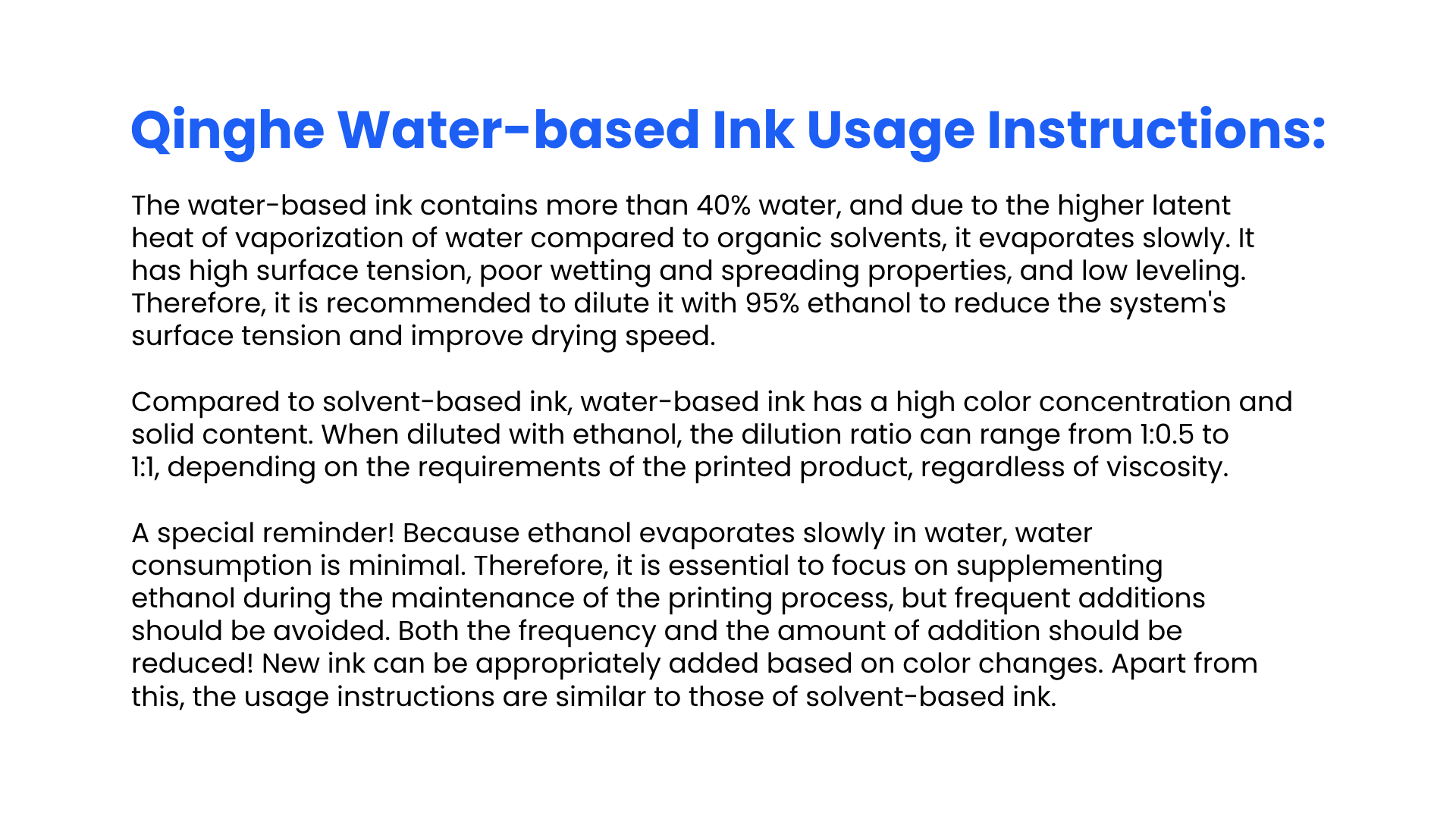
Superior Quality of Water-Based Ink for Plastic Printing
Water-based ink stands out for its exceptional quality when it comes to plastic printing ink. Its ability to penetrate and adhere to plastic surfaces results in sharp, vibrant prints that resist fading and cracking over time. The smooth finish achieved with water-based ink enhances the overall appearance of the printed design, making it the top choice for high-quality plastic printing.
Environmental Benefits of Using Water-Based Ink
Water-based ink offers a more sustainable alternative to traditional solvent-based inks for plastic printing. Here are some of the key environmental benefits of using water-based ink:
- Reduced Air Pollution and Health Risks: Water-based inks contain significantly lower volatile organic compounds (VOCs) levels than solvent-based inks. VOCs contribute to smog formation and can irritate the eyes, nose, and throat. By minimizing VOC emissions, water-based inks create a healthier work environment and reduce the overall impact on air quality.
- Easier Cleanup and Disposal: Water-based inks are easier to clean up with soap and water, eliminating the need for harsh solvents that can harm the environment. Water-based ink residue is also considered non-hazardous waste, simplifying the disposal process.
- Lower Energy Consumption: Water-based inks often require lower curing temperatures during printing than solvent-based inks. This translates to reduced energy consumption, leading to a smaller carbon footprint and a more sustainable printing process.
Switching to water-based ink for plastic printing offers a multitude of environmental benefits. From cleaner air and safer workplaces to lower energy usage and simpler waste management, water-based inks represent a significant step towards a more sustainable future for the printing industry.
Regulatory Compliance with Water-Based Ink for Plastic Printing
In today's environmentally conscious landscape, regulatory compliance is crucial when choosing the right ink for plastic printing. Water-based ink meets strict environmental regulations and safety standards, ensuring businesses comply with industry guidelines and avoid potential fines or penalties. By using water-based ink, companies can demonstrate their commitment to sustainability while meeting legal requirements.
Why Screen Printing with Water-Based Ink is Ideal for Plastic
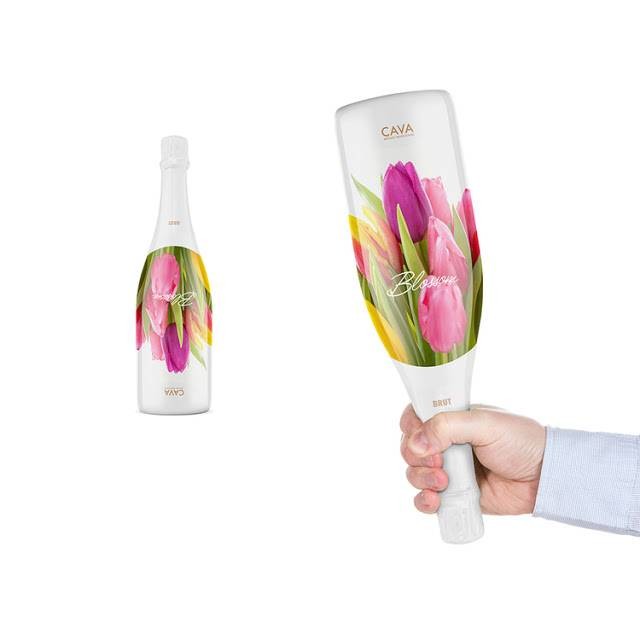
Water-based ink offers unparalleled versatility when it comes to screen printing on plastic. This type of ink can be used on various plastics, from rigid to flexible, making it suitable for various applications such as packaging, signage, and promotional items. Its ability to adhere well to different types of plastic ensures that the printed designs will remain vibrant and sharp over time.
1. Versatility of Water-Based Ink for Screen Printing on Plastic
Water-based ink is known for its adaptability to different types of plastic substrates. Whether it's PVC, PET, or polystyrene, this ink can provide excellent adhesion and coverage without compromising the integrity of the plastic material. This makes it ideal for screen printing on various plastic products, including bottles, containers, and displays.
2. Durability and Longevity of Water-Based Ink on Plastic
One of the key advantages of using water-based ink for screen printing on plastic is its long-lasting durability. The ink forms a strong bond with the plastic surface, resulting in prints resistant to abrasion and fading. This means that designs printed with water-based ink will maintain their vibrancy and clarity even after prolonged use or exposure to environmental elements.
3. Vibrant and Crisp Results with Water-Based Ink on Plastic
Water-based ink delivers exceptional color saturation and sharpness when used for screen printing on plastic. The ink's high pigmentation ensures that designs appear vivid and eye-catching, making them stand out on any plastic substrate. Whether it's intricate patterns or bold graphics, water-based ink can produce stunning results that meet the highest standards of quality and aesthetics.
By choosing water-based ink for screen printing on plastic, you can achieve remarkable versatility in substrate compatibility while ensuring long-lasting durability and vibrant results that make your designs pop!
The Unmatched Performance of Plastisol Ink for Plastic Printing
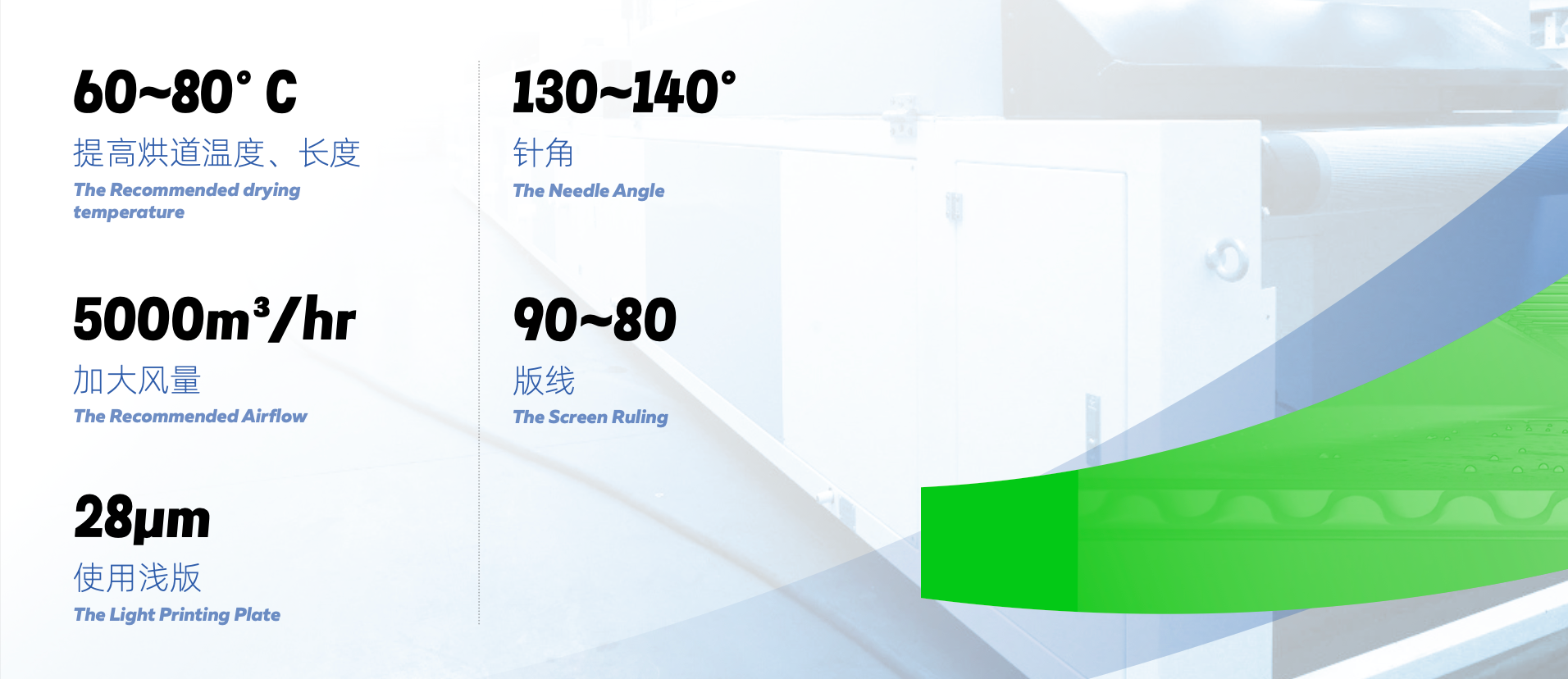
Plastisol ink is renowned for its exceptional adhesion and coverage for plastic printing. Its unique formulation allows it to adhere seamlessly to the surface of various types of plastic, ensuring a smooth and even application. This results in vibrant and long-lasting prints that stand the test of time, making it a top choice for plastic printing ink.
Enhanced Adhesion and Coverage with Plastisol Ink
Plastisol ink boasts superior adhesion properties, ensuring it adheres firmly to the plastic surface without flaking or peeling off over time. Its thick consistency allows for complete coverage, producing sharp and vivid prints that pop on any plastic substrate. Thus, plastisol ink is the go-to choice for achieving high-quality and durable prints on plastic materials.
Flexibility and Stretchability of Plastisol Ink on Plastic
One of the standout features of plastisol ink is its remarkable flexibility and stretchability on plastic surfaces. This makes it ideal for printing on flexible PVC banners, silicone phone cases, or even sports equipment made from various plastics. The ink moves with the material without cracking or distorting, ensuring the print maintains its integrity even under stress or movement.
Applications of Plastisol Ink for Different Types of Plastic
Plastisol ink's versatility extends to its ability to be used on various plastics, including polyethylene, polypropylene, PETG, acrylics, and more. Whether it's rigid or flexible plastics, plastisol ink delivers exceptional results. This type of plastic printing ink offers unmatched performance across diverse applications, from promotional products to industrial components.
With its unparalleled adhesion and coverage capabilities, along with its flexibility and versatility in application across different types of plastics, plastisol ink stands out as a top choice for achieving high-quality prints on plastic materials.
Exploring the Potential of Textile Ink for Printing on Plastic
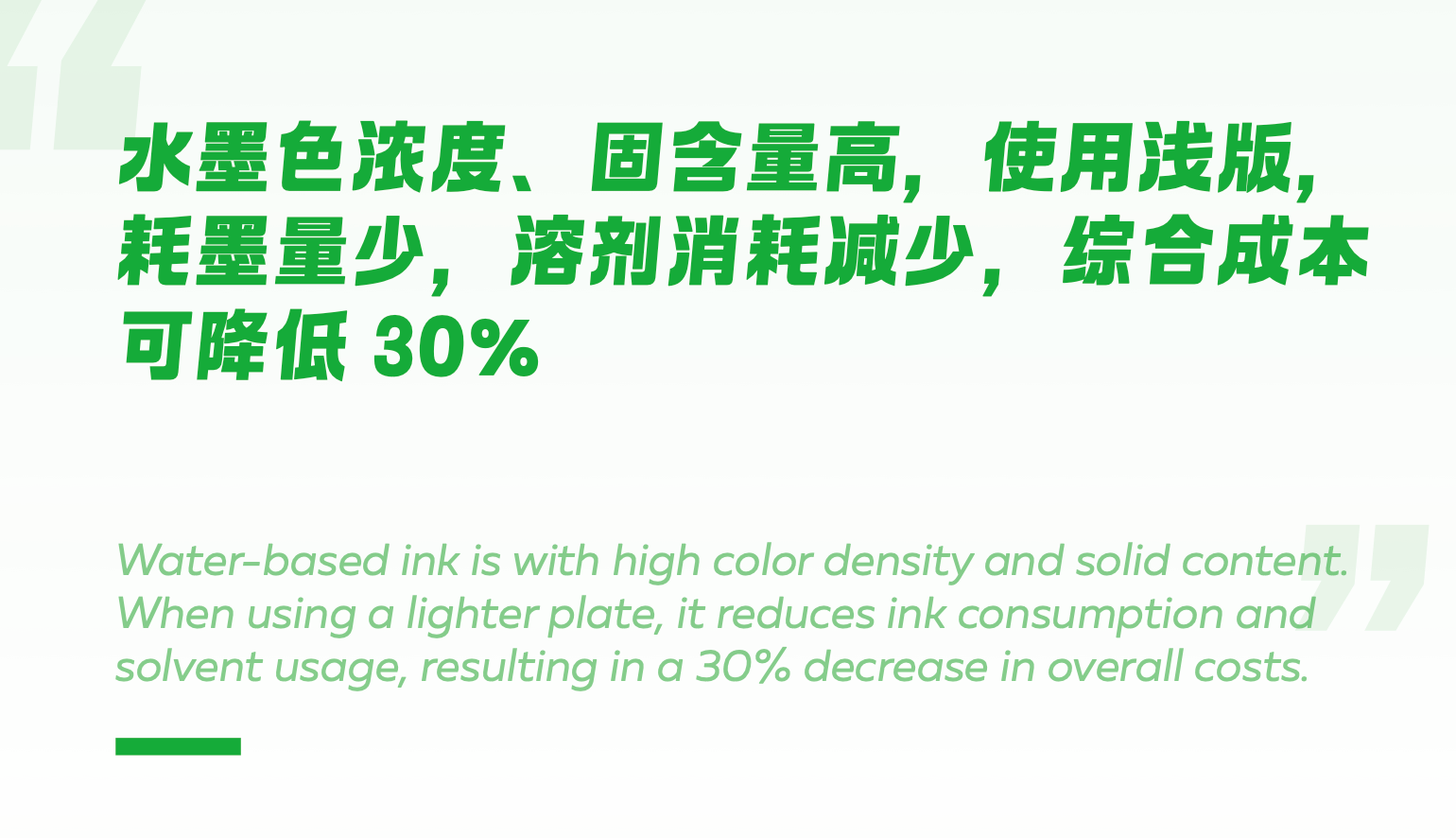
When it comes to plastic printing, textile ink may not be the first choice that comes to mind, but its compatibility and adaptability are worth exploring. Textile ink has unique properties that make it ideal for achieving desired effects on plastic. It offers a range of opportunities and challenges for those willing to experiment with this unconventional choice.
Compatibility and Adaptability of Textile Ink for Plastic Printing
Textile ink may seem out of place in plastic printing, but its compatibility and adaptability are surprisingly impressive. Its ability to adhere to various types of plastic surfaces makes it a versatile option for those looking to expand their printing horizons beyond traditional inks.
Unique Properties of Textile Ink for Achieving Desired Effects on Plastic
Textile inks, traditionally used for fabric printing, offer surprising advantages when applied to plastics. These inks possess unique properties that unlock a world of creative possibilities for plastic decoration. Here's how textile inks can elevate your plastic printing projects:
- Textured Finishes: Forget flat and boring! Textile inks can create raised textures, adding a tactile dimension to your design. Imagine incorporating Braille-like patterns or simulating fabric textures like linen or canvas.
- Soft Touch Appeal: Textile inks often have a softer feel compared to traditional plastic inks. This creates a luxurious and inviting user experience, making your plastic product stand out.
- Vivid and Durable Colors: Many textile inks boast exceptional color vibrancy and can withstand exposure to light and washing better than some plastic inks. This ensures your design retains its brilliance over time.
You can transform ordinary plastic into visually stunning and captivating products by harnessing the unique properties of textile inks. Next time you want to add depth and intrigue to your plastic creations, consider the possibilities textile inks offer.
Opportunities and Challenges of Using Textile Ink for Plastic Printing
While there are opportunities to explore textile ink in plastic printing, venturing into uncharted territory also comes with challenges. From mastering the application process to understanding how different plastics interact with textile ink, there's no shortage of learning curves when working with this unconventional medium.
Now, let's delve into best practices for printing ink on plastic as we navigate the complexities and possibilities of different types of ink.
Best Practices for Ink Printing on Plastic
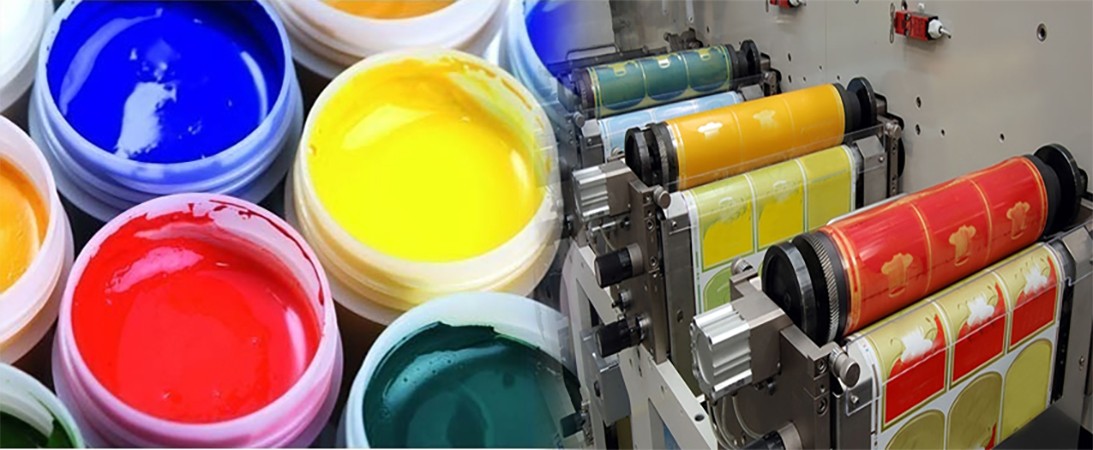
Key Considerations for Successful Printing with Ink on Plastic
When it comes to plastic printing ink, it's crucial to consider the compatibility of the ink with different types of plastic substrates. Understanding the plastic's surface tension and adhesion properties is essential for successful ink printing. Proper curing and drying processes should also be considered to ensure optimal results.
Tips for Achieving Optimal Results with Plastic Printing Ink
When printing on plastic, using the right materials and techniques is crucial for achieving crisp, long-lasting results. Here are some key factors to consider:
- Match Your Equipment to the Ink: For screen printing, choose the right mesh count for the ink viscosity. For digital printing, ensure your nozzle size is compatible with the ink type.
- Maintain Optimal Ink Conditions: Proper ink viscosity and temperature control are essential. The correct viscosity allows smooth ink flow, while the right temperature ensures proper drying and adhesion.
- Test and Refine: Conduct thorough print tests to assess ink performance on your specific plastic substrate. This will help you identify any adjustments needed for consistent, high-quality results.
- Achieve Accurate Color: Utilize a color-matching process to ensure your printed colors accurately reflect your design.
By following these tips, you can ensure your plastic prints are vibrant, durable, and professional-looking.
Overcoming Common Challenges in Printing with Ink on Plastic
One common challenge in plastic printing is achieving good ink adhesion to the substrate. To overcome this challenge, adhesion promoters or surface treatment methods can significantly improve ink adhesion on various types of plastic. Additionally, proper cleaning and maintenance of printing equipment are essential to prevent issues such as ink buildup or clogging during the printing process.
Choose Water-Based Ink: A Sustainable Solution for Plastic Printing
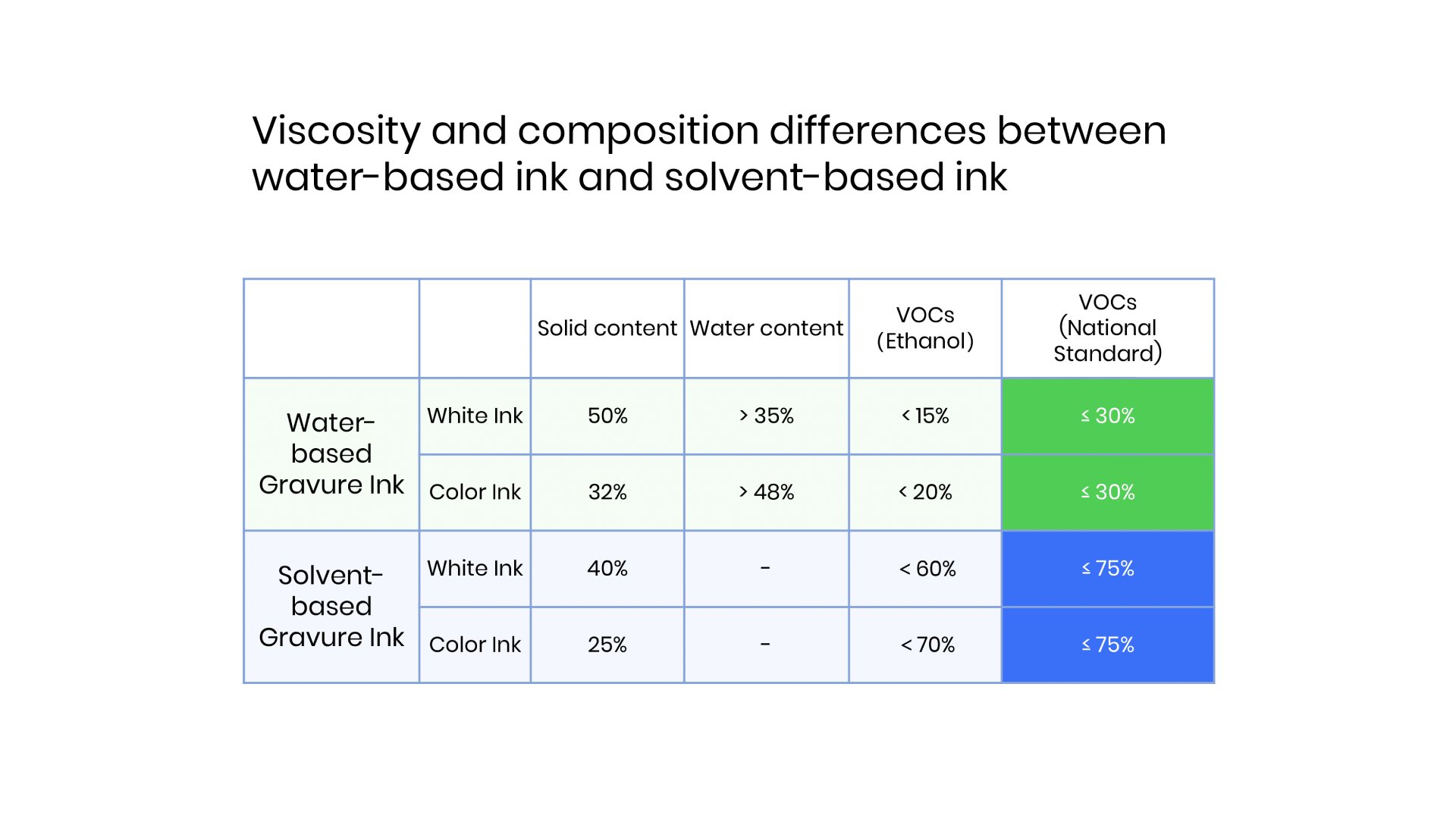
Water-based ink offers a sustainable solution for plastic printing by reducing environmental impact and ensuring regulatory compliance. Its eco-friendly properties make it the preferred choice for businesses committed to sustainability and responsible manufacturing practices.
Elevating Plastic Printing with Water-Based Ink Innovation
The continuous innovation in water-based ink technology has elevated the standards of plastic printing, offering superior quality, vibrant results, and unmatched durability. Businesses can now achieve exceptional print outcomes while reducing their environmental footprint.
Embracing the Future of Plastic Printing with Water-Based Ink
Embracing water-based ink for plastic printing is essential as we move towards a more sustainable future. By adopting this innovative solution, businesses can meet regulatory requirements while contributing to a cleaner environment and achieving outstanding results in their plastic printing projects.